From Earth to the Moon: Firefly Aerospace’s Path to Space Innovation and Affordability
The aerospace industry is a dynamic sector that plays a crucial role in advancing technology and exploring the frontiers of space. In recent years, the rise of private space companies has transformed the landscape, making space more accessible than ever before.
Firefly Aerospace is part of this exciting industry, developing small and medium-sized launch vehicles to cater to the growing demand for commercial space launches.
Based in Cedar Park, Texas, Firefly is dedicated to increasing access to space for various users and aims to contribute to the broader goals of innovation and exploration within the aerospace sector.
Expanding Horizons: Firefly Aerospace’s Mission to Democratize Space
Firefly Space Systems began as a small startup in January 2014. It was founded by Tom Markusic, P.J. King, Michael Blum, and a group of entrepreneurs who funded the company themselves.
By that time, the company had grown to 43 employees and invested in a significant expansion by acquiring 215 acres of land for an engine test and manufacturing facility in Briggs, Texas, located about 50 miles north of Austin.
In its early days, Firefly focused on developing new technologies. They bought fiber-winding equipment to make composite cryotanks using a special out-of-autoclave process. In mid-2014, they tested these prototype tanks at NASA’s Marshall Space Flight Center.
Firefly Aerospace wants to make space available to everyone. Their goal is to break down barriers that have made space exploration difficult. By building affordable and reliable rockets, Firefly helps small and medium-sized payloads reach space easily and cost-effectively.
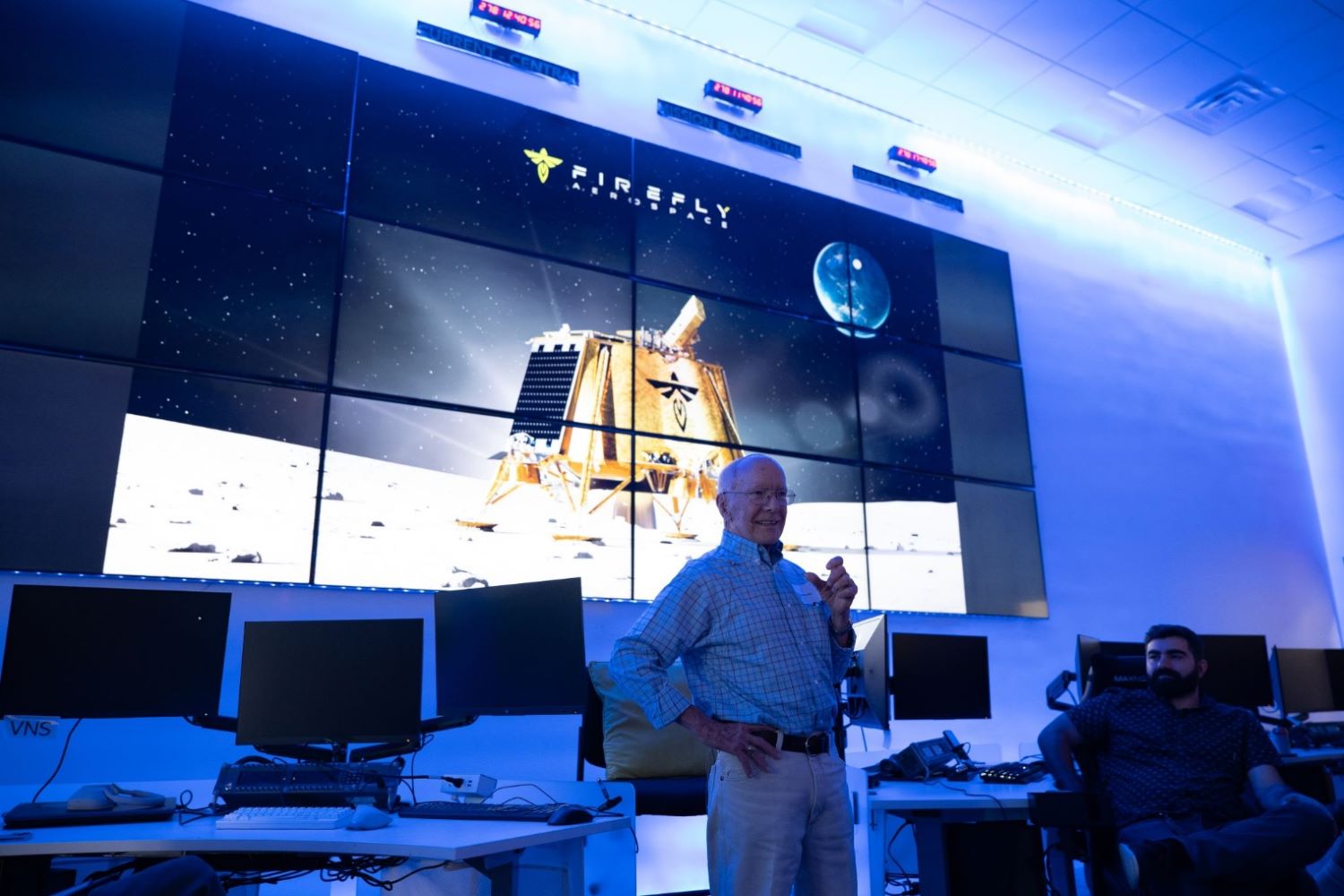
Firefly believes that space shouldn’t just belong to a few big companies. It should be open to everyone – startups, schools, and smaller countries. This belief drives Firefly to come up with new ideas and solutions that make it cheaper for anyone to explore space.
“As an end-to-end space transportation company, Firefly Aerospace is on a mission to enable our world to launch, land, and operate in space – anywhere, anytime. Our small- to medium-lift launch vehicles, lunar landers, and orbital vehicles provide affordable, responsive, and reliable space access for government and commercial customers,” the company stated.
Firefly’s Flagship Products: Leading the Way in Space Innovation
Firefly Aerospace is at the forefront of space innovation with its cutting-edge products designed to meet the diverse needs of the space industry. Their key products include the Alpha launch vehicle, the Blue Ghost lunar lander, and the Elytra space tug.
Alpha Launch Vehicle: Affordable Access to Low Earth Orbit
The Alpha launch vehicle is Firefly’s cornerstone product, engineered to deliver small to medium-sized payloads to low Earth orbit (LEO). With a payload capacity of up to 1,000 kilograms to LEO, Alpha is designed to offer a cost-effective alternative to traditional launch vehicles.
Alpha can be launched domestically or internationally through Firefly’s launch facilities at the Vandenberg Space Force Base in California and new launch capabilities coming soon at the Mid-Atlantic Regional Spaceport (MARS) on Wallops Island, Virginia as early as 2025 and at the Esrange Space Center in Sweden as early as 2026.
Its affordability is a game-changer for startups, educational institutions, and smaller nations looking to access space. The vehicle’s design incorporates advanced materials and technologies, such as lightweight carbon composite structures and efficient Reaver engines, which enhance its performance and reliability.
“When we conceived Alpha from the beginning, we’re already targeting to go quick and be able to actually load the tank and fly as fast as possible,” said Jordi Paredes Garcia, Alpha Chief Engineer at Firefly Aerospace.
Blue Ghost Lunar Lander: Firefly’s Gateway to the Moon
The Blue Ghost lunar lander is an exciting project from Firefly Aerospace that supports lunar exploration and scientific research. It has been chosen by NASA for the Commercial Lunar Payload Services (CLPS) program, showcasing its important role in future lunar missions.
Blue Ghost is designed to carry up to 150 kilograms of payload, making it a versatile option for different lunar missions. Its advanced navigation and landing systems ensure precise and safe landings, which are vital for successful lunar operations.
Throughout the mission, Blue Ghost provides essential resources like data, power, and thermal management to its payloads, from the journey to lunar orbit to activities on the Moon’s surface.
A standout feature of Blue Ghost is its ability to operate during the lunar night, which is important for longer missions. The lander can also conduct sample return missions, helping gather valuable data and materials for scientific research.
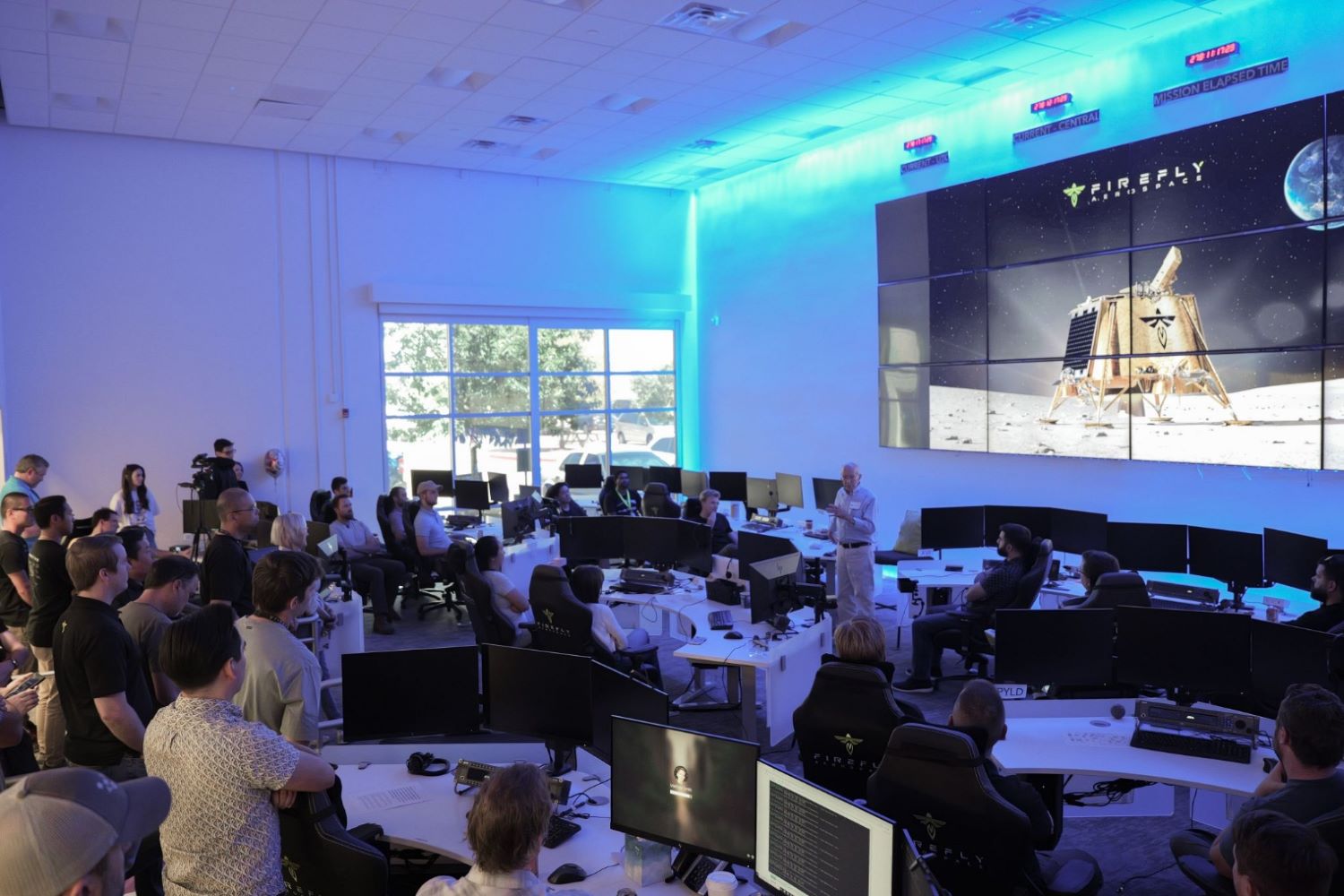
Firefly’s first Blue Ghost mission, named “Ghost Riders in the Sky,” is scheduled for launch in Q4 2024. This mission will deliver 10 scientific instruments and technology demonstrations to the lunar surface as part of NASA’s CLPS initiative.
In addition to its initial mission, Firefly has secured multiple task orders through the CLPS initiative, totaling over $230 million in awards for Blue Ghost missions planned for 2024 and 2026.
Elytra Space Tug: Enhancing On-Orbit Capabilities
Elytra is designed to support all stages of government and commercial missions. It offers various services, including satellite deployment, repositioning, and servicing. Its design enables it to perform complex tasks in space, such as transferring payloads between different orbits and conducting in-space repairs.
Elytra’s versatility is shown in its three different models: Elytra Dawn, Elytra Dusk, and Elytra Dark. Each model is tailored for specific missions and environments.
Elytra Dawn is optimized for LEO and can be launched quickly for urgent missions. It supports rideshare and delivery tasks, providing multiple on-demand deployment options for customers.
Elytra Dusk is designed for larger, more complex missions, operating from LEO to geosynchronous orbit (GEO). It offers improved maneuverability, power, and autonomy, handling tasks like relocation, space monitoring, and deorbiting.
Elytra Dark is built to withstand tough conditions and serves as a reliable orbital platform. It can support transfers from LEO to lunar orbit and beyond, working alongside other vehicles for advanced space monitoring and servicing.
Firefly’s Elytra vehicles utilize many of the same flight-proven components from Firefly’s launch vehicles and landers, including carbon composite structures, core avionics, and propulsion systems.
How Firefly Aerospace Achieves Rapid Launch Capabilities
Firefly Aerospace is a leader in quick launch capabilities thanks to its new technologies, efficient processes, and smart infrastructure. Let’s look at how Firefly makes fast launches possible.
Designed for Speed: Enhancing Launch Responsiveness
From the outset, Alpha was conceived with speed and efficiency in mind. This required making several critical design decisions early on. For instance, the quick disconnect lines, fill lines, and vent lines were all sized to facilitate rapid fueling and detanking.
One of the challenges in achieving such rapid responsiveness is balancing the need for quick operations with the constraints of mass and performance. Larger lines and valves can speed up the fueling process but add weight to the vehicle, which can reduce the payload capacity.
Jordi Paredes Garcia, Alpha Chief Engineer at Firefly Aerospace, explained that they had to make trade-offs to ensure that the rocket could be filled and detanked quickly without compromising too much on performance.
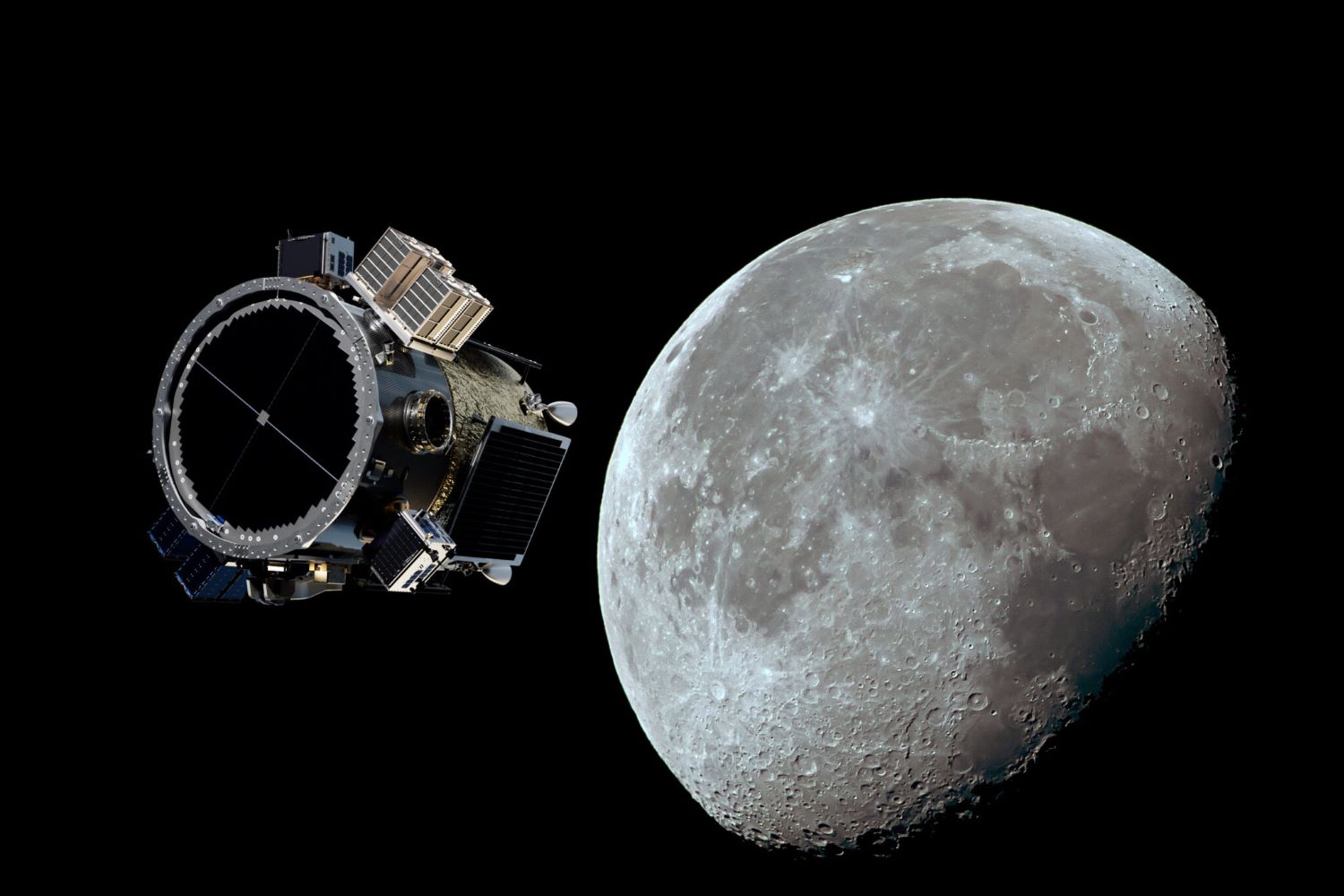
“If I could load it in 18 hours, I could go very slowly and fill it up. Things would be lighter. But then you gotta make that trade. It’s like, okay, I’m having lines and valves and components that I can take to orbit and not do too much performance, but still at the same time be able to fill and detank quickly,” said Jordi.
Another important consideration is the operational constraints related to crew work hours. Operators cannot work more than 12 hours a day, so the entire process of loading, detanking, and preparing for a potential scrub and reattempt the next day must fit within this timeframe.
This requirement necessitates a highly efficient process to ensure that the crew can rest and be ready for another attempt if needed. Jordi mentioned that they are continually refining their procedures to improve timing and efficiency based on their experiences with each launch.
Managing the temperatures of the fuel and oxidizer is another critical aspect of the process. Unlike some other companies that supercool their liquid oxygen to gain extra performance, Firefly opts for a more straightforward approach.
They load the liquid oxygen at standard cryogenic temperatures and allow it to vent to achieve the desired pressure and temperature. This method provides greater flexibility, allowing the team to hold and wait, if necessary, without having to detank and scrub the mission for the day.
“If we want to hold and wait, you can hold and wait. If you’re super cool because you have to go through a liquid nitrogen system, you can load and then you have more performance,” said Jordi.
Firefly Aerospace’s Efficient Load and Go Method
Firefly Aerospace is balancing performance and launch availability with a strategy called “Load and Go.” This method uses larger fuel and oxygen lines to fill their tanks faster. While this adds some weight and slightly reduces performance, it greatly improves their ability to launch on short notice.
Firefly also makes different choices regarding propellant temperatures. Unlike SpaceX, which uses supercooled propellants for better performance, Firefly skips the supercooling step to simplify the process.
This decision helps solve a major logistical challenge in the space industry: dealing with potential launch scrubs caused by unexpected events, like a fishing boat entering the exclusion zone during propellant loading.
For SpaceX, such delays can be critical because their supercooled propellants can’t stay at the right temperature for long. They begin loading propellants just 35 minutes before liftoff in a process called “load and go.”
If there’s a delay, the propellants can warm up, lose performance, and possibly lead to a mission scrub if they no longer meet the required standards.
In 2016, a Falcon 9 rocket exploded on the launch pad while loading propellants. It was carrying a $2 billion Facebook satellite, and the explosion was caused by a buckled metallic liner in the pressure vessel.
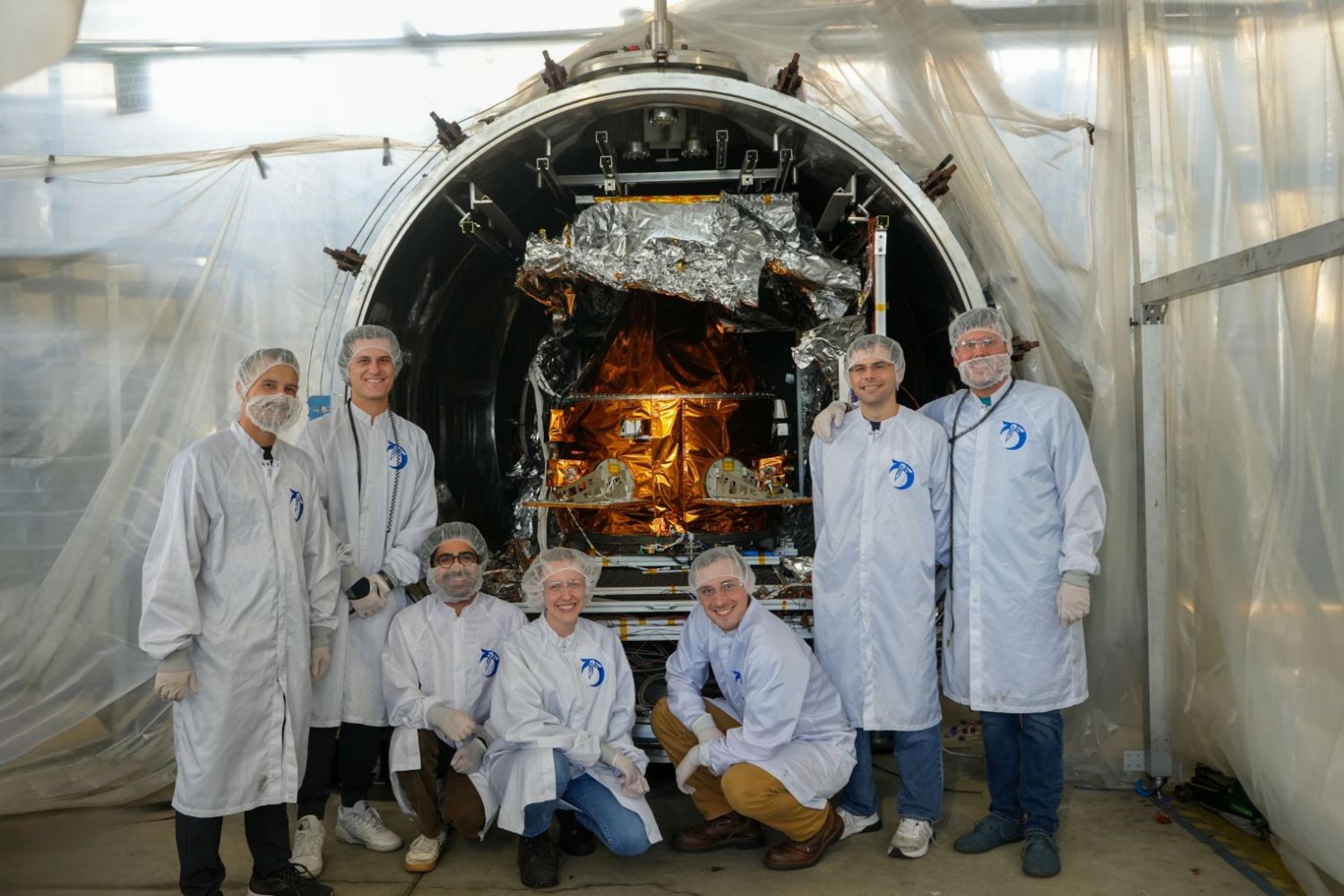
Firefly’s method, unlike one that requires a seven-hour wait, utilizes warmer propellants that can be continuously replenished as they evaporate, maintaining consistent performance.
When ground equipment failed, the launch was aborted, but Firefly simply reset the countdown timer and tried again shortly after, topping up the propellants. Although they did not resolve the ground equipment issue before the launch window closed, they had another opportunity the next day.
Efficient Testing for Quick Launches: Inside Firefly Aerospace’s Engine Innovations
Brigette Oakes, the Vice President of Engineering at Firefly Aerospace, noted the importance of efficient engine testing in their rapid development process.
“We have six different test stands that test anything from components to full vehicle stages as well as composite structures,” she stated.
Brigette explains that they are currently testing a development engine, having just hot-fired it the previous day after swapping out some components. The team is focused on two main goals: improving the performance of the Reaver engine and enhancing the reliability of the main valves. They are particularly looking at different injector designs to increase efficiency.
“Firefly is the first company that’s actually flown this engine cycle to orbit and successfully. So, what I mean by tap-off engine cycle, there are a couple different open cycles that companies will use,” Brigette Oakes shared.
In a traditional gas generator cycle, an additional combustor operates at a different mixture ratio to drive the turbine. In contrast, Firefly’s tap-off cycle siphons off a portion of the gas from the main combustion chamber to drive the turbo pump. This reduces complexity and weight.
Brigette acknowledges that the tap-off design, while simpler and more efficient, has its challenges. The engine is “bootstrapped,” which means it needs some combustion in the main chamber to start the turbine.
“On the ground, we can do that differently than in flight. And that startup sequence is pretty sensitive. So, trying to figure that out. We were able to iterate on that pretty quickly to tune that in,”
Firefly Aerospace: Shaping the Future of Space Technology Through Innovation
Firefly Aerospace is recognized for its groundbreaking contributions to space technology, constantly expanding the limits of what can be achieved. The company’s dedication to innovation is clear across several critical areas.
Rocket Engine Cycles: How Firefly Aerospace Innovates for Efficiency
A rocket’s engine cycle explains how it transfers propellants – fuel and oxidizer – from their tanks to the combustion chamber. The simplest way to do this is through pressure feeding, where high pressure pushes the fuel and oxidizer into the combustion chamber when valves are opened. However, this method can limit performance.
To generate more thrust and be more efficient, engines need to deliver fuel and oxidizer at higher volumes and pressures.

For example, SpaceX’s Merlin engine uses a gas generator cycle. In this system, some of the propellants are partially burned in a separate chamber, and the exhaust gases from this process drive a turbine that pumps the rest of the propellants. However, this method is wasteful because the exhaust gases are simply released.
In contrast, Firefly’s Reaver engine uses a different method. It captures hot, expanding gases straight from the combustion chamber and sends them into a turbine to power the turbopump.
The Advantages of Pintle Injectors in Modern Rocket Engines
Pintle injectors are a simpler and more cost-effective option compared to the complex injectors used in the Saturn V program.
The Saturn V injector was huge, needing 2,832 precisely drilled holes – 1,428 for oxidizer and 1,404 for fuel. These holes created jets that mixed and atomized the propellants, but the complicated design was expensive and had issues with combustion instabilities.
Combustion instabilities happen when pressure waves and vibrations increase due to heat from combustion, potentially disrupting engine performance or causing failures. The Saturn V’s F-1 engine faced several problems during development because of this.
To help, engineers added wedges to the injector plate to break up these pressure waves.
This simpler design not only lowers manufacturing costs but also provides benefits for Firefly’s tap-off engine cycle. The shape of the pintle injector creates two zones in the combustion chamber.
The central zone, rich in fuel, helps mix any unburned fuel, while the outer zone creates a cooling film along the chamber walls. Firefly uses gases from this outer zone to power the turbopump, improving both performance and efficiency.
Turbo Pump Design at Firefly Aerospace
Firefly Aerospace has made an improvement in turbo pump design by taking gas directly from a cooler part of the combustion chamber. This prevents the turbine blades from melting.
By doing this, they remove an extra component from their engine, making the system simpler. For engineers, having fewer parts means less weight, lower manufacturing costs, and fewer chances of something going wrong.
However, this innovative approach does come with its own set of challenges. One concern is the risk of combustion instability, which can lead to uneven performance. Fortunately, Brigette Oakes, Firefly’s VP of Engineering, noted that they don’t experience these instabilities with their design.
Another issue arises from the nature of their fuel, RP-1, a type of hydrocarbon. When using a fuel-rich mixture, soot can form as a byproduct. Since the gas driving the turbo pump comes directly from the combustion chamber, soot can accumulate on the turbine wheel over time.
This buildup can degrade the performance of the engine during flight, as it reduces the size of the orifices in the turbo pump, impacting thrust.
“The longer you’re flying, the more soot you’re building up on that turbine inlet, which reduces your performance and, so there’s also some really interesting proprietary technologies that we’ve developed and also patented that help us, not have that issue,” said Brigette.
Firefly Aerospace’s Composite Breakthrough
Firefly Aerospace has made a major achievement with its Alpha rocket, which boasts the largest all-composite liquid oxygen tank in the world. This innovation means they can do away with the usual metallic liner, making the tank about 20% lighter than traditional designs.
However, building linerless cryogenic tanks is challenging, especially because they need to handle the very low temperatures of liquid oxygen, which can drop to around -300°F.
To ensure safety and reliability, Firefly employs an acceptance testing plan. Each tank undergoes pressure testing with liquid nitrogen, where it is subjected to loads above what it will experience during flight.
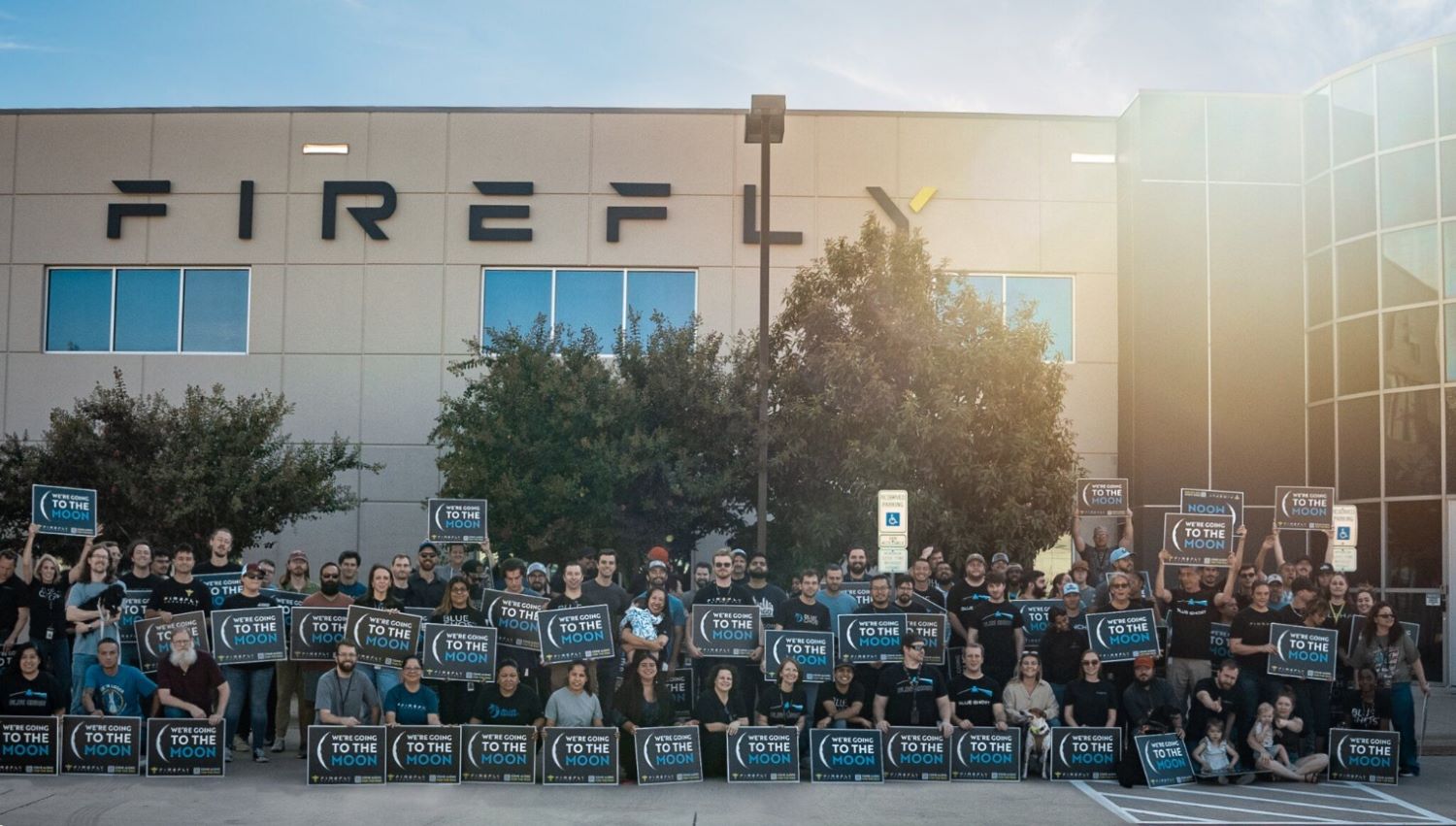
Jordi also mentioned the complexities of designing such large composite structures. The manufacturing process requires extensive analysis and testing, as different layers of carbon fiber must be laid out at various angles to ensure strength against pressure, compression, and shear loads.
While other companies have utilized composites, Firefly stands out for its capability to create large cryogenic tanks, a feat that has required years of refinement and innovation in material science.
Cork: Essential Material in Firefly Aerospace’s Rocket Design
Firefly Aerospace uses a thin layer of cork to protect their rockets from heat, making sure the carbon materials stay cool.
Jordi, the chief engineer, explains that this cork is lightweight and inexpensive, which is why it’s commonly used in the industry. However, he wishes they could eliminate cork entirely because it adds about 700 pounds of glue, cork, and paint to the rocket.
“My dream as a chief engineer is to get rid of all the cork. It takes a long time and it’s heavy,” Jordi stated.
The cork creates a thermal gradient, helping to lower temperatures by around 100°F, depending on its thickness. This is especially important before the first flight, as engineers need to ensure safe temperatures across different rocket stages.
Jordi notes that sourcing cork isn’t hard; it’s available in sheets. Although there are talks about a potential cork shortage, he finds it practical for startups trying to keep costs down, especially since they don’t plan to reuse it after launch.
He points out that cork is made from tree bark, which kids often use for crafts, but in this case, it helps keep rockets from burning. However, installing the cork can be time-consuming, which is a challenge as they look to ramp up production for multiple rockets efficiently.
Jordi shared, “You can buy different thicknesses and it’s cheap. The thing is, it’s annoying to install, like it takes time. And if you want to increase production, that’s one that we’re trying to find ways to actually speed up the process. You know, you want to go to like six, twelve, twenty-four rockets, right. Laying this takes time.”