How These Leading Specialty Contractors “Up the Ante” by Embracing Innovation?
The construction industry is one of the largest global markets and contributors to the economy. It accounts for more than 680,000 employers and approximately 7 million employees in the US alone. Meanwhile, specialty contractors play a pivotal role in the industry, bringing in $750 billion in estimated annual revenues across 450,000 employers in the United States.
As general contractors and owners seek expertise in plumbing, electrical work, welding, and other fields to bring their projects to life, the demand for specialty contractors continues to rise. Specialty contractors are experiencing unprecedented growth and success on a national and global scale. While people’s perception of this industry is more of a traditional practice than an inventive one, construction innovations are advancing rapidly, with 29% of firms are investing in technology to supplement worker duties. These investments in innovations pay off significantly; the United States Chamber of Commerce shares that 70% of contractors believe advanced technologies increase productivity, improve schedules, and enhance safety.
With more and more contractors prioritizes innovations in their business, it’s critical to understand how they leverage technology to go ahead of the game. Let’s unveil the innovation mindset from these seven top specialty contractors below to understand their trajectory to success.
#1: ACCO Engineered System – Full Tech Stack Drives Success
ACCO Engineered Systems, an employee-owned company based in Pasadena, California, is a leading environmental firm. ACCO was founded in 1934 as an HVAC company. Over the last 86 years, the specialty contractor has expanded to include plumbing, process piping, sheet metal, skid manufacturing, industrial piping, building automation controls, and mechanical services.
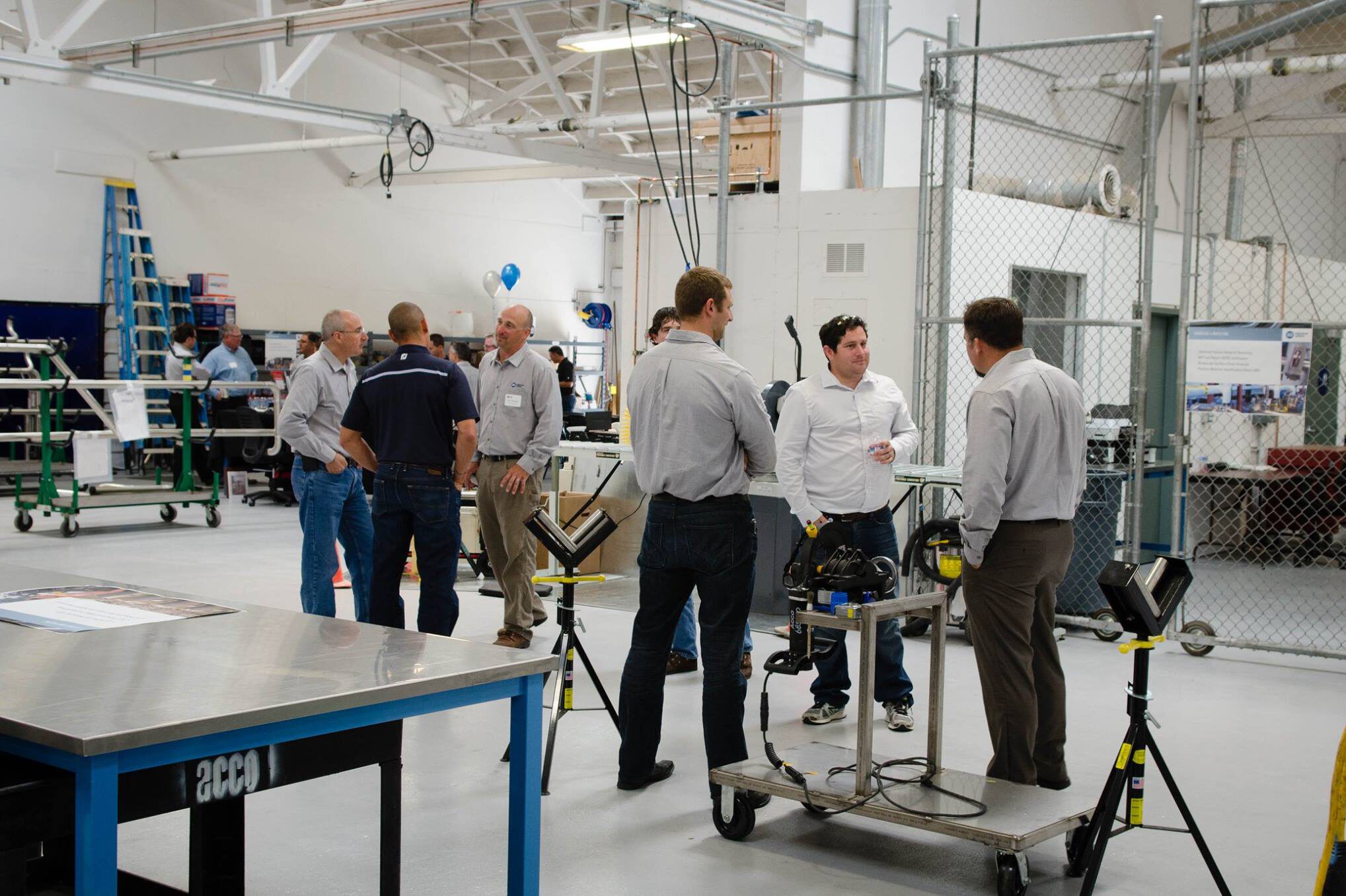
The company utilizes Building Information Modeling (BIM) to bridge the gap between engineering and construction. The technology allows ACCO to cross-collaborate across departments, improve workflows, and eliminate costly rework.
ACCO’s, BIM Manager, Steve Whitmer, recently spoke with Autodesk about his passion for BIM and using technology for complex projects. He shared that BIM is central to operations at ACCO and its data management. The technology supports the company as a whole as Whitmer explains, “It started for us in construction and engineering, but there is not any reason why BIM cannot be spun out to the other specialties. That is what really excites me about the future of BIM. In this digital era, there is no reason why we cannot take more value out of this data that is sitting in models and expediting workloads.”
ACCO’s technology suite contains many more tools such as Virtual Design and Construction (VDC) and three-dimensional CAD visualization software. These tools help general and subcontractors coordinate on HVAC, process, and plumbing projects from any location.
#2: Comfort Systems – Prefabrication Focus Leads to Efficiency and High Quality
Public company Comfort Systems provides commercial HVAC, mechanical, and electrical contracting services to businesses of all sizes across the United States. Comfort Systems has approximately 12,000 employees and revenues over $2 billion.
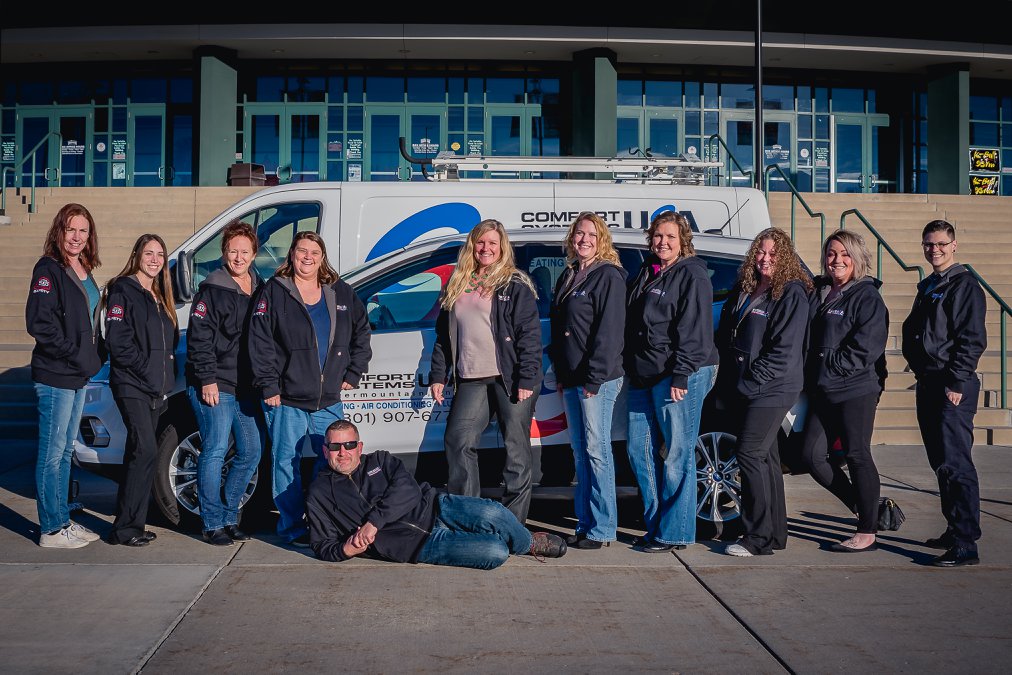
The company’s construction and manufacturing teams work together and rely on prefabrication “to deliver the best quality and most efficient HVAC system possible, including spool fabrication and custom pipe fittings.” Prefabrication allows Comfort Systems to reduce costs, increase efficiency, and offer affordable price points to customers.
The prefabrication of these system parts is done at the company’s Chandler, Arizona facility. Their multilayered strategy includes the use of a coordinated model to validate estimates, set prefabrication goals for the shop, installation goals for the field, plus the Fabrication Suite of Products and BIM. Each component works together to deliver winning bids at a rapid pace.
#3: Rosendin – Early Adopters of Change and Innovation
It’s hard to talk about electrical contractors and not mention Rosendin Electric. The San Jose-headquartered and employee-owned company is the nation’s largest private electrical contractor. Rosendin has weathered the Great Depression and World War II throughout its 101 years. What’s remained constant is a focus on using the latest technology. Being an early adopter of technology has paid off as Rosendin has annual revenues of approximately $2 billion.
Key adoptions include BIM technology in 2008 and mobile construction apps to support their remote workforce. Sam Lamonica, Rosendin’s then Electric CIO, spoke about the company’s remote workforce technology back in 2014, “Our people work in all sorts of remote regions so we needed to create a Mobile First environment where employees could choose their own devices, a CYOD model that would support all the latest devices on any of the carriers.”
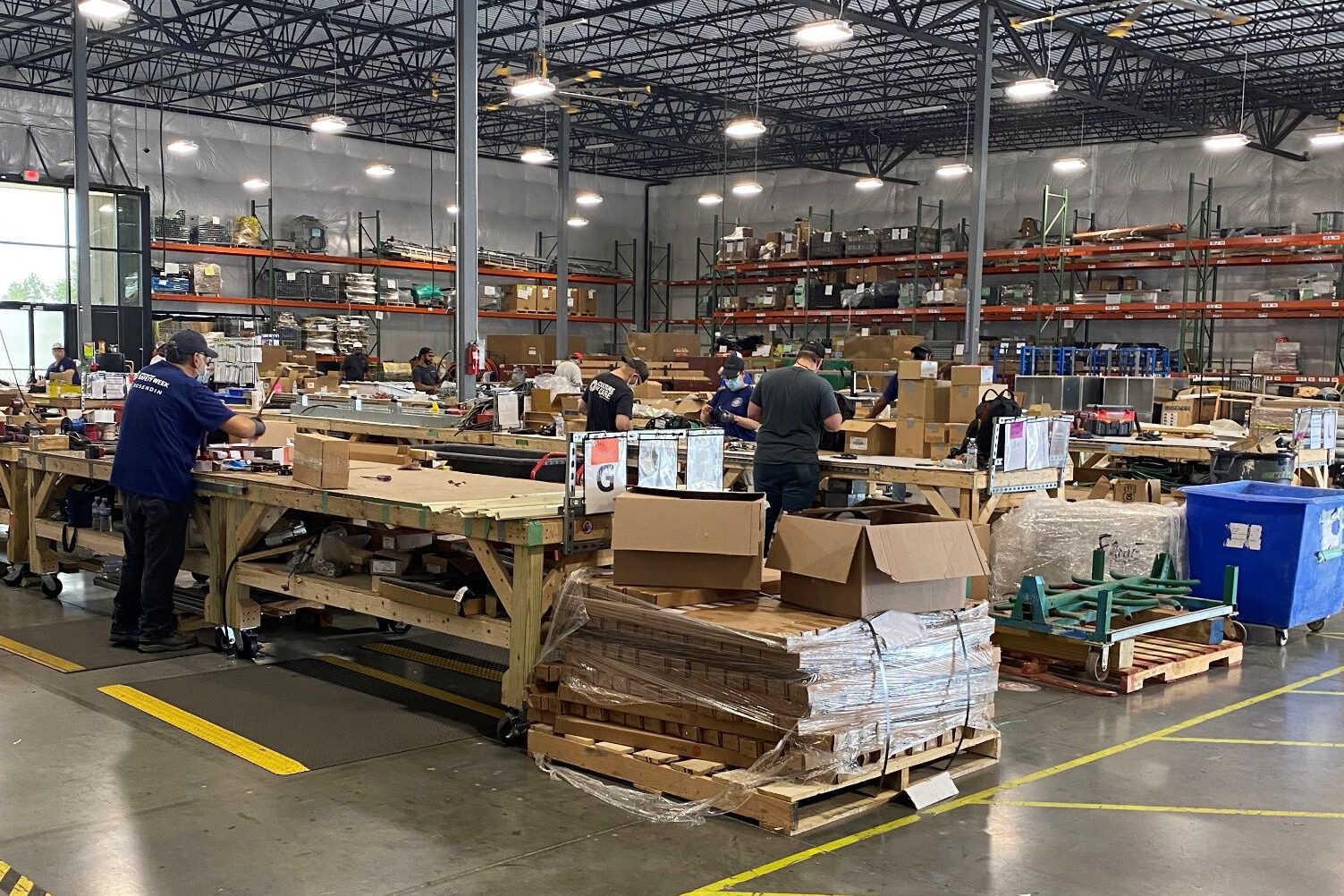
Being ahead of the curve has certainly served the company well as the workforce has shifted significantly to a remote working model in recent months.
Rosendin continues to prioritize “the most proven and effective technologies” to deliver an “ongoing commitment to innovation.” This commitment extends into the larger community as well. Rosendin worked alongside other general contractors and subcontractors to transform 1940s auditorium buildings in Coachella Valley into medical facilities for COVID-19 patients. The large-scale project included:
- Retrofitting and updating electrical systems in California’s Riverside County Fairgrounds buildings to transform them into medical facilities
- Upgrading and creating a backup power scheme in the event of an outage
- Developing safety protocols for the above jobsites
#4: Mckinstry – Bucking Conventional Wisdom of Digital Transformation
This Seattle-based company with over 60 years into the market has always been the national leader in designing, constructing, operating and maintaining high-performing buildings. With over 1,600 professional staff and trades people throughout the United States and operations in more than 15 states, McKinstry leads the construction market with its “ahead-of-the-game” vision for adopting technology.
Dean Allen, the company’s CEO, believes that the key to his team’s success lies in defying the conventional along the way. The company’s effective digital transformation isn’t just about adopting new tools but also developing a new way to track and measure the performance of its initiatives.
The company understands that the structure of many AEC firms isn’t conducive to technology adoption. IT departments are often disconnected from high-level business objectives, which makes execution difficult. What’s more, calculating the ROI of technology — plus measuring the opportunity costs of not adopting tech — isn’t a clear-cut task.
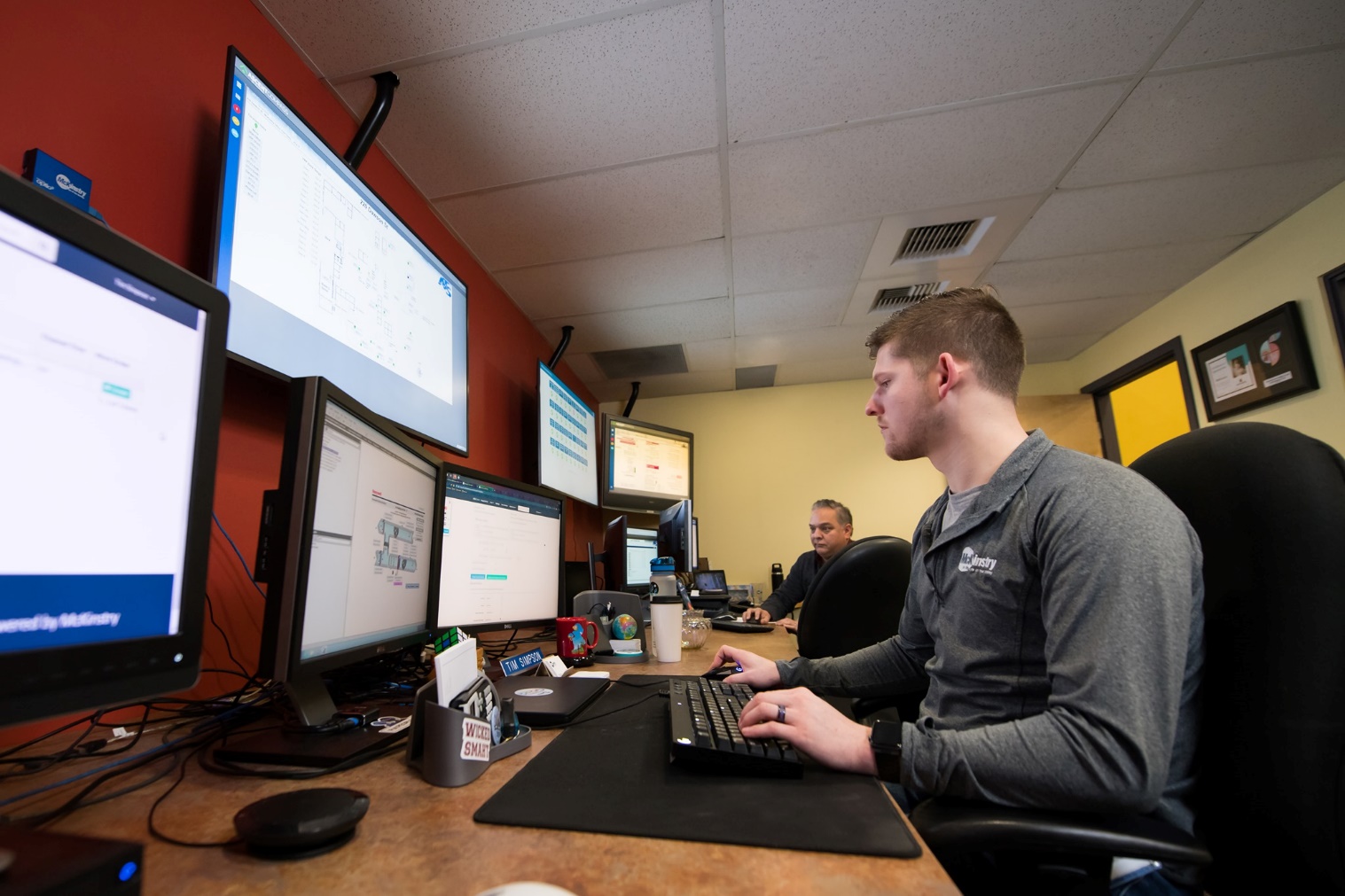
McKinstry has a way to address this with their Product Management Organization (PdMO) which acts as a strategic organization to smoothen the company’s digital workflows. This adoption gives them a framework for innovation with enough structure and predefined processes to be effective in executing projects. They’re able to develop products, or technology solutions, on the fly with minimal business disruption.
In addition to their Product Management Organization, McKinstry is leading a variety of projects that enable their teams to innovate and expedite digital construction workflows.
Such projects include MSUITE, a cloud-based shop management platform designed to connect BIM, Fab, and field construction teams or McKinstry’s 2020 Construction Hackathon, a two-day event involving 50 employees across multiple backgrounds and departments. The Hackathon encouraged participants to come up with innovative solutions to minimize waste in design and construction. “Contrary to conventional wisdom of not being on the bleeding edge and jumping on the latest technology, we would like to be an early adopter” – Allen said.
#5: Mark III – Streamline Workflows through Innovation
Founded in 1967, Mark III has evolved from a single-trade electrical contractor to a MEP construction and service company delivering projects across California. With a culture steeped in the idea of better, Mark III is on a continual quest to evaluate and implement new technology and processes to improve outcomes and transform project delivery.
To streamline how contractors interact, Mark III vertically integrated teams to deliver a one-stop-shop solution to increase collaboration and coordination to deliver higher quality projects, while decreasing schedule and cost.
“With a turnkey solution in place for all MEP services, we wanted to continue our journey and take manufacturing for construction to the next level by finding a way to have greater predictability on projects to eliminate waste and increase quality,” says Makayla Oei, Project Executive at Mark III Construction.
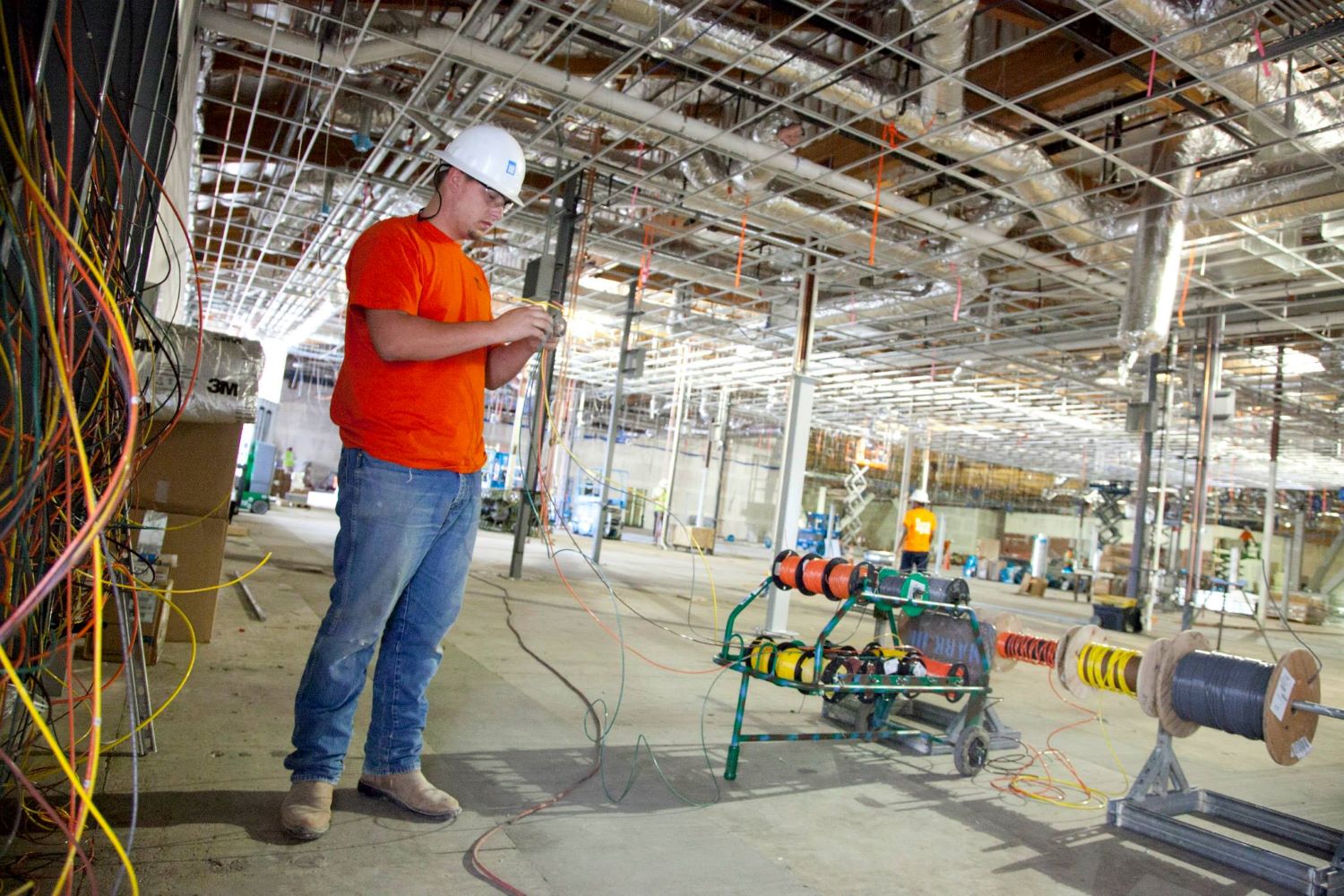
In line with Mark III’s mission of “leading the evolution of construction,” the firm developed Project Mountain — a self-funded research and development initiative that aims to streamline and improve how projects are planned, designed, and built.
Project Mountain allowed for the development and testing of standardized repeatable units of kitted wall systems with multigrade racking assemblies for a hospital corridor to replace conventional stick-build methodology. The second innovation effort, Project Mountain II, leveraged virtual technology, standardization and manufacturing to develop manufactured MEP wall panels for a typical medical office building exam room.
Early estimates indicate that Mark III’s medical-sector customers can save an average of 16% to 21% on MEP wall-framing costs while reducing field installation to a fraction of the time as compared to stick-build construction, thereby cutting construction schedules by as much as 20%.
Project Mountain gives Mark III a creative outlet to change the traditional approach to construction and expose the world to a new way of building. By automating tasks and creating deeper coordination across teams with technology, Mark III can add more value to improve project outcomes and develop stronger partnerships with GCs and Owners.
The team at Mark III is excited to bring more innovation to the industry. With the sky’s the limit attitude, the team is continuing to drive change and adopt technology to deliver better projects to clients.
“Project Mountain provides an avenue to challenge yourself and test your limits,” says Oei. “There are days when I am scared, and I don’t know how things will go, but if you’re not scared, you’re not challenging yourself enough. And that’s what yields the greatest results.”
#6: The Conti Group – Foster Entrepreneurship to Sustain over a Century
With over a century in the market, The Conti Group which headquartered in New Jersey has evolved from a four generation, family-owned construction company to a diversified firm representing various industries including engineering, renewable energy, real estate, technology and beyond. The company prides itself to foster “entrepreneurial mindset” albeit its base on engineering and construction.
“We constantly seek new ways to do old things”, said the CEO Kurt Conti. “We use hardware and software to improve efficiency and production. In another sense, we use old ways to solve new problems.” For example, Conti Federal Services company focuses on disaster response after hurricanes, tornados and other natural disasters. Managing crucial tasks in these situations is not very different from supply chain and workflow management for construction projects. However, advancements in robotic, drones and artificial intelligence enable Conti Group with enormous capabilities to improve both responsiveness and proactivity.
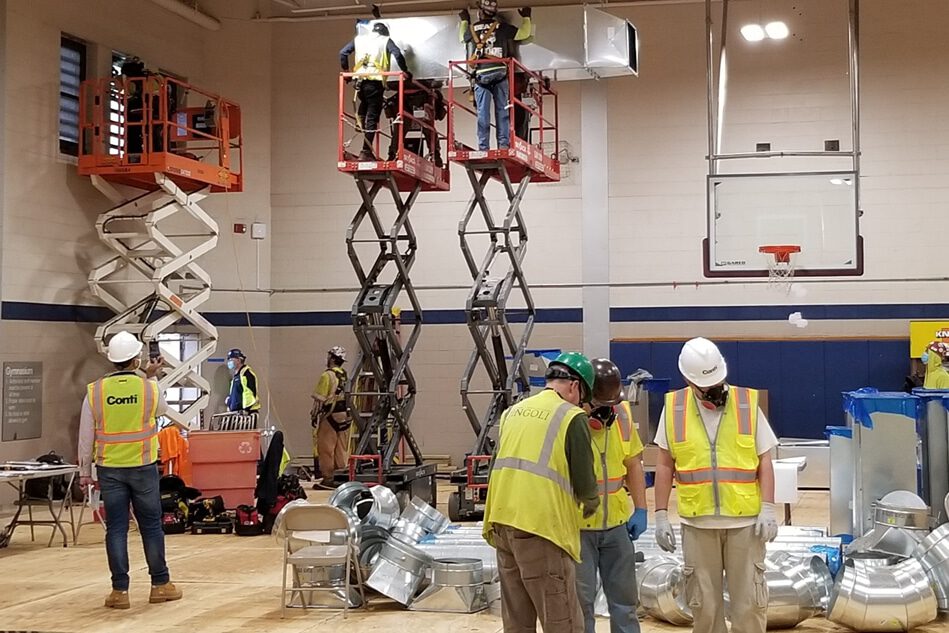
The firm also levels up its technology integration by establishing Tenna – an IoT company that provides the first comprehensive platform for construction companies to find, track and manage all their physical data assets. By connecting assets machine-to-machine, the Conti Group’s latest investment opens almost unlimited possibilities, especially when considering the amount of infrastructure that is needed and is being built worldwide.
Kurt believes that his team’s constant focus on innovation is what enables Conti Group to thrive through a 112-year period of incredible change. “At Conti, we always striving to evolve. We recognize that the successful businesses twenty years from now may be very different from the successful business of today. As a result, we’re always challenging our people to be proactive, pursue new opportunities, and embrace changes as a means to grow” – he said.
#7: Cupertino Electric – Building Leaders through Training and Tech
Cupertino Electric, Inc. is a private electrical engineering and construction company headquartered in San Jose, California. Founded in 1954 in its namesake city of Cupertino, the company has grown to employ over 3,800 field and office workers throughout the Western United States.
The company does more than provide electrical installation, engineering, and energy services. Cupertino also builds data centers for some of the world’s largest tech companies, supplying the infrastructure needed to innovate.
Known for their commitment to workforce development, Cupertino Electric focuses on “delivering technically-complex projects fast without compromising quality or safety.” They achieve this goal in part by developing leads through their Foreman Development program. “The most significant thing we’re doing to get our next-level leaders up to speed quickly is continuing to invest in our Foreman Development program that builds leadership skills from within company ranks,” says the CEO Tom Schott. He says the firm provides defined training and development opportunities for both field and office employees that allow them to grow their skills and lead others “so that we have an available bench of talent.”
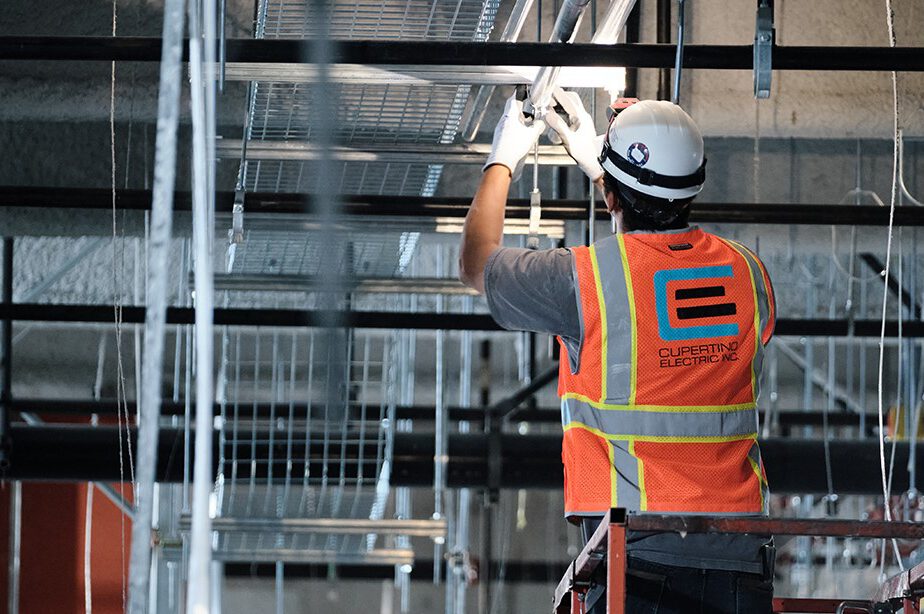
Nick McComb, Superintendent at Cupertino Electric, is a great example of the company’s commitment to leadership development. Beginning as an apprentice, McComb rose the ranks to superintendent through positions as journeyman wireman, foreman, general foreman, and site superintendent. Cupertino’s investment in its workers certainly pays off as employees develop the skills they need to solve challenges through training and technology.
It’s no wonder that elevate technology is one of the most pivotal concern for employees at the company. “Many in construction are resistant to technology, especially some of our older generation builders and electricians. While it may be easy to think, “this is how we’ve always done it and it’s worked,” some of the tools that are coming out now are world changing. Although I agree with some of that mentality, the overall trend with most of this technology is very positive.” – Nick believed.
Innovation Drives Future
Sub and general contractors alike continue to build innovation into their strategies to overcome obstacles and innovate in new markets. While specialty contractors will certainly face new challenges this year and beyond, it’s safe to say that the winners will include continuous improvement and early adoption of emerging technologies in their toolkits. As the top specialty constructors are heading their minds towards the latest innovation and constantly adapt themselves to changes, the rest in the construction industry have no reason not to follow suit.