Dallas on the Fast Track: Overcoming Construction Roadblocks
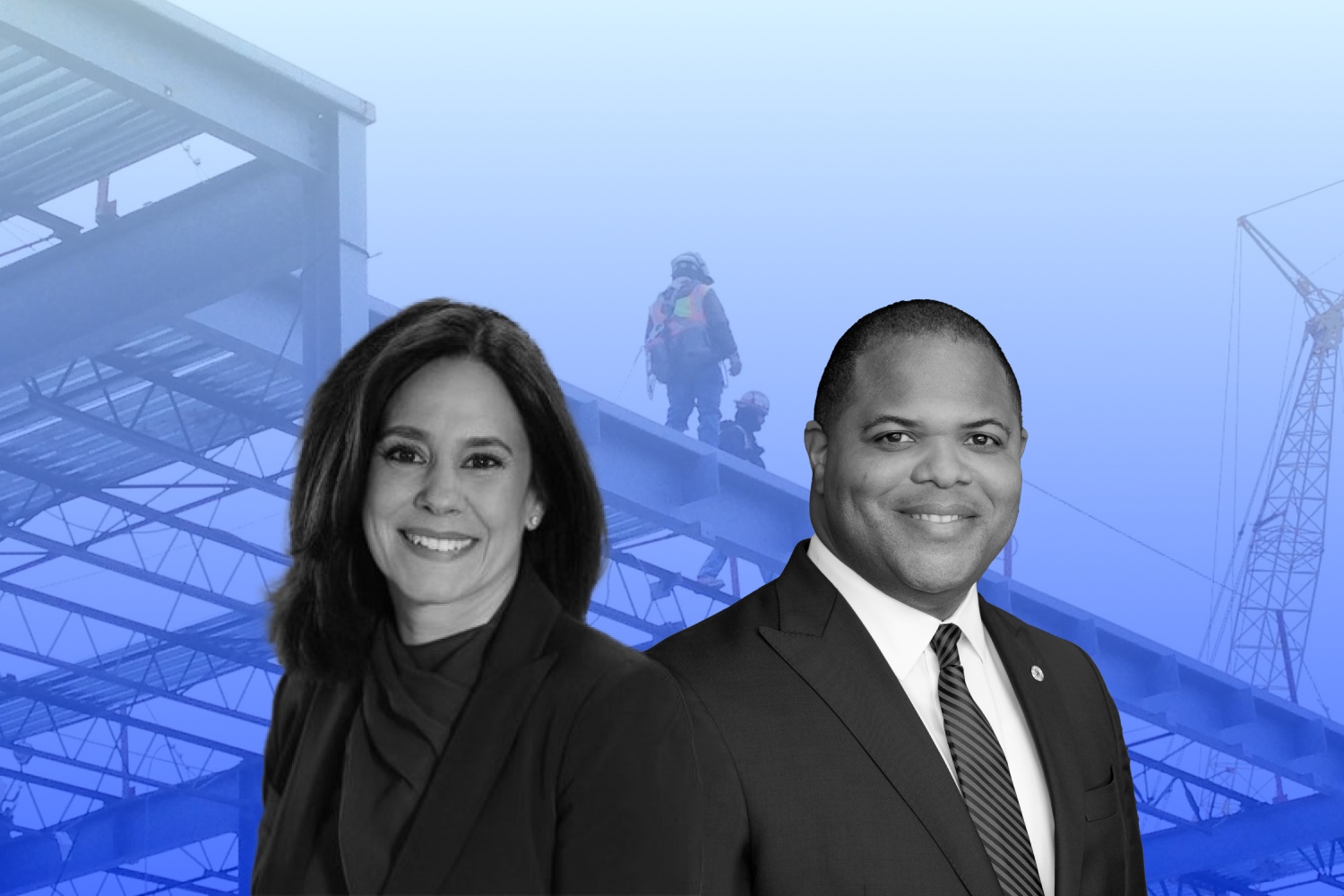
According to Bankrate’s nationwide survey, mortgage rates reached their highest level since 2000 in August 2023.
The average rate on 30-year home loans last topped this mark in December 2000, as shown by Bankrate research. That was before the September 11 terrorist events prompted the Federal Reserve to lower interest rates, and long before the Great Recession compelled the Fed to keep rates low.
While mortgage rates momentarily surpassed 7% in late 2022, they fell this year as investors banked on an economic slump. The dramatic drop in mortgage rates reflects the Fed’s continuous battle against inflation, as well as a recent downgrading of US government debt and the lessening likelihood of a recession.
Rising loan rates and record housing prices are making it impossible for many Americans to buy a home, leaving builders less optimistic that they will be able to sell it if they build one. Dallas, one of them in the front row, has been in terrible discomfort.
Sluggish Construction Activity in a Promising Homeland
It’s not until the Federal Reserve decided to hike up interest rates that hit the construction industry badly, cause the pandemic has thrown the first punch.
The COVID-19 problem appears to be hastening the ecosystem’s disturbance, which began long before the crisis.
When the coronavirus shutdowns began, construction projects were seen as critical corporate activity.
Despite the fact that residential and commercial builders were pushing ahead with existing projects, the flow of new construction business was decreasing.
By 2020, about 40% of contractors nationwide reported that project owners had paused or terminated current construction projects due to the sinking economy.
“The abrupt plunge in economic activity is taking a swift and severe toll on construction,” Ken Simonson, chief economist with the Associated General Contractors of America, said in a just-released report. “The sudden drop in demand stands in sharp contrast to the strong employment levels this industry was experiencing.”
Dallas-Fort Worth has set such a fast pace for industrial construction and has maintained it for so long, that perhaps it’s natural to wonder how long it can last.
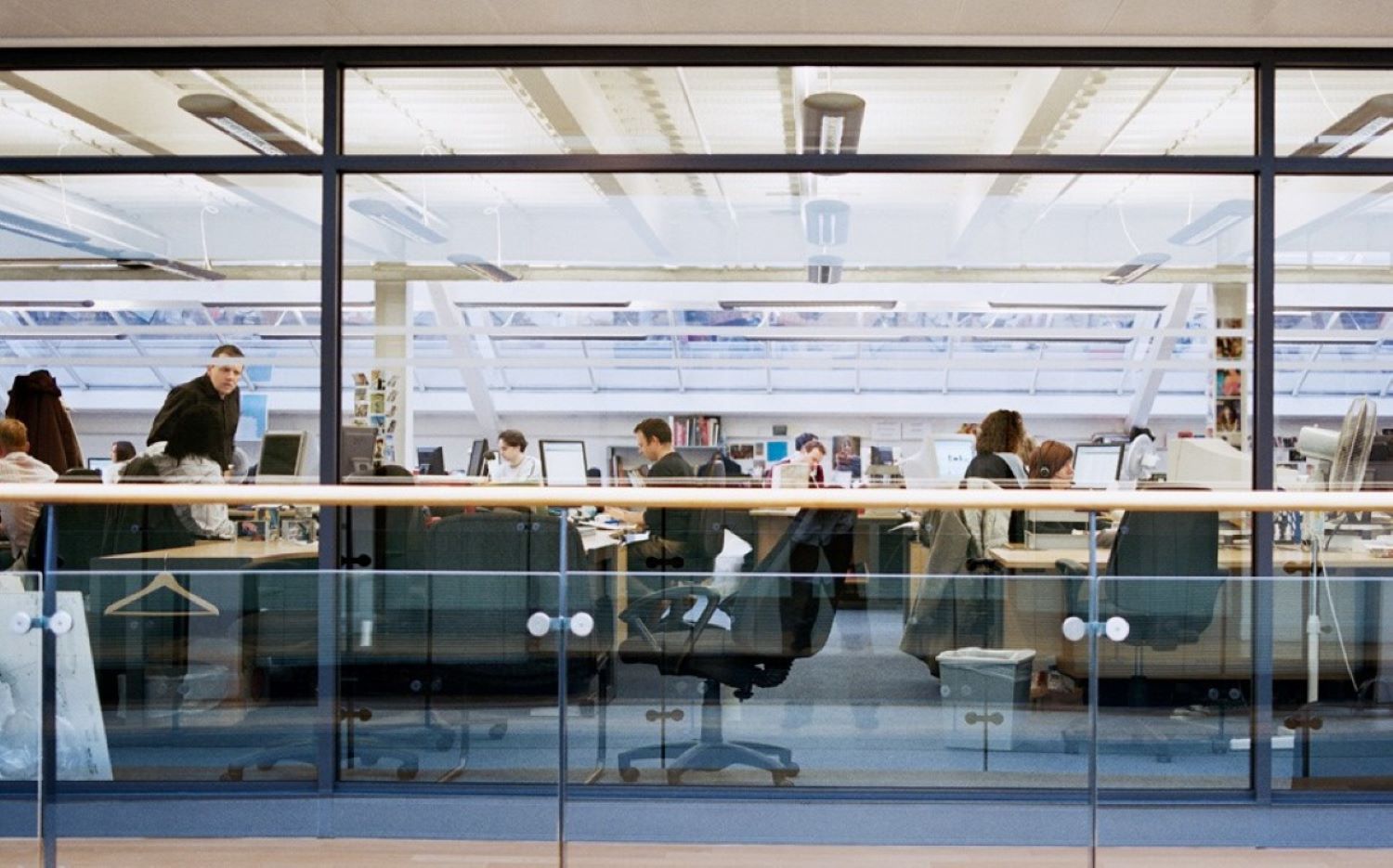
According to the CoStar Analytics industrial outlook for 2022, the region not only led the nation with 61.1 million square feet of industrial space under development as of December 2021, but it also represented 12% of all industrial construction in the United States.
There are plans for new developments of all kinds, including Perimeter Park, a 297,628-square-foot, two-building industrial complex in Dallas, and I-20 Logistics Park, a 1.01-million-square-foot warehouse facility in southern Dallas County.
Meanwhile, projects like the one-building speculative industrial site at Sunnyvale West Business Center and the additional space at Fort Worth Logistics Hub are in the works.
According to Cumming, a global project management and cost consultancy organization, commercial development should total $3.81 billion in 2022, slightly less than the $3.89 billion total in 2021. Manufacturing construction is expected to cost $1.288 billion, up from $1.289 billion in 2021.
“Now is a time for cautious optimism,” said developer Eric Langford of Langford Property Co. “The dynamics are very good here but they’re plateauing some nationally.”
Surmounting Challenges – Anticipating Better Days on the Horizon
Despite some setbacks, the Dallas-Fort Worth building business is thriving. Langford observed that supply chain issues are generating significant wait times for materials such as steel, gypsum, and lumber.
“You have to order steel 12 to 18 months out,” he said. “The process is longer than it used to be and it’s harder to get a slot.”
Developers and contractors often must pre-pay for materials like dock levelers and order them sooner. “We will order them ahead of time, stockpile them and use them when we need them,” Langford said.
According to the findings of a recent industry survey conducted by the Associated General Contractors of America and Sage, only 10% of construction contractors nationwide have reported no significant supply chain issues.
Even fewer contractors, only 8%, reported having no problem hiring workers, while 83% reported having difficulty filling some or all paid or hourly craft positions. Three out of every four respondents believe that hiring will remain difficult or become more difficult this year.
Furthermore, 84% of respondents stated that costs were higher than expected. In a separate analysis of government data, the AGC calculated that material prices soared 20% in 2021.
Nonetheless, according to AGC’s business outlook report for 2022, 74% of construction firms plan to hire in 2022 due to rising demand for most types of projects. Among projects those in the industry are most bullish on, warehouses tied with “other health care” for the highest expectations among predominantly private-sector categories, with a net of 41% each.
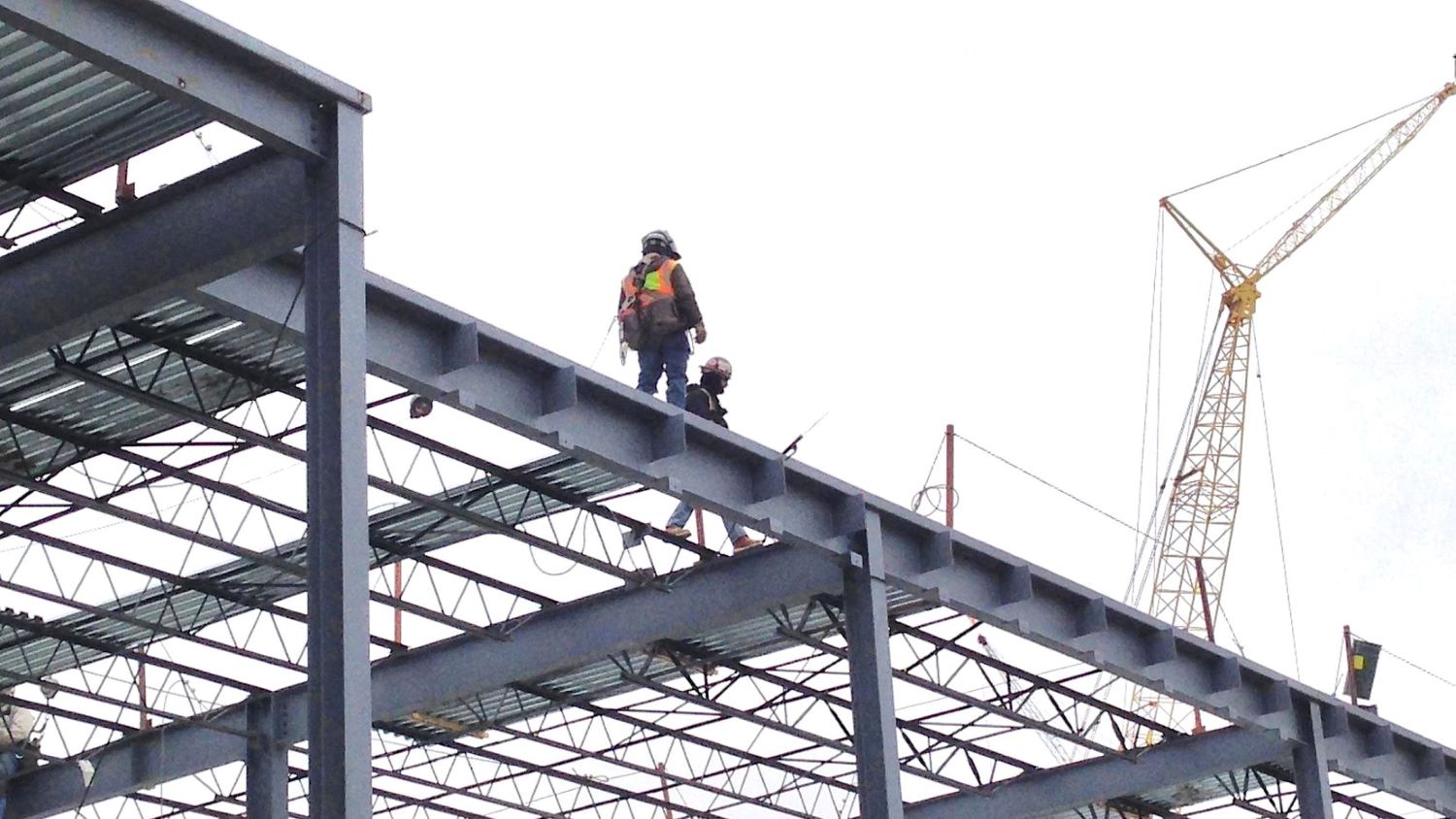
But even with the effort in hiring, the workforce shortage still make projects take longer and cost more, and look set to worsen in 2023. According to the survey, 69% of contractors anticipate to employ in the coming year, while only 11% expect to shrink their headcount. To encourage workers, 72% increased base pay rates over 2021, while about a third enhanced rewards and perks.
Despite these efforts, 80% of employers are now experiencing problems hiring workers, and the majority of respondents expect this to continue. Furthermore, 83% of contractors are concerned that the shortage and ensuing unskilled skilled labor pool may jeopardize the safety and health of their employees – by far the most serious hazard mentioned by respondents.
Cultivating new workers will take time and effort, according to Pittsford, Vermont-based Casella Construction co-founder John Casella.
As contractors in the United States prepare for the coming year, COVID-19 continues to have an impact on the industry, particularly supply chains. Contractors are becoming less confident about private sector jobs as inflation and the threat of a recession continue to loom.
Builders have reason to be concerned: 36% of respondents had projects canceled or postponed but not rescheduled last year. Rising costs were cited as the primary factor for around half of the initiatives. Overall, the group got 1,032 answers, the majority of which were from general contractors.
Although contractors are optimistic overall, that doesn’t mean there aren’t rocky times ahead, said AGC Chief Economist Ken Simonson in a webinar.
“Even when we’ve had recessions or slow growth expectations for the economy, contractors are by nature optimists,” Simonson said. “But it is notable that in nearly all of these categories, particularly on the private side, contractors have lower net positive readings or deeper negative readings than they did in previous years.”
Generally, we observe an image featuring both bright and dark areas. Regional agents, builders, and construction workers anticipate a prosperous year ahead for the commercial real estate sector. In most cases, residential properties are progressing as planned, but certain construction sites are experiencing delays due to a scarcity of transformers.
These devices are utilized, for instance, to change electricity generated by large generators into a usable form for handheld tools. This presents an opportunity to focus on a global issue at a local level. Transformers are manufactured using copper wiring, and there’s a worldwide shortage of copper projected to persist throughout the remainder of the decade.
Counter New Issue – Copper Shortage Haunting the Construction Work
For thousands of years, copper has played an important role in the global economy. The Bronze Age? That occurred when blacksmiths discovered how to forge copper with tin.
Copper is now employed in electrical and heating equipment due to its chemical qualities, which make it such a good conductor. It’s found in automobile engines, household plumbing, washing machines, and a variety of other everyday items.
Not to mention the various copper alloys that are blended into other metals and objects. Moreover, copper is an incredibly recyclable metal, with the majority of the world’s copper still residing in the Earth’s crust.
In fact, only approximately 12% of the total copper available on Earth has been extracted throughout human history, and nearly all of it continues to circulate. It’s even possible that some of the copper currently in circulation once served as jewelry or armor in ancient Egypt.
Regarding the construction of buildings, copper plays a crucial role in the building industry, and constructing 20 buildings would require a substantial quantity of this metal. Copper is widely employed in construction due to its strength, durability, and low heat and electrical conductivity.
The quantity of copper necessary for constructing 20 buildings would depend on factors such as the size and purpose of each structure. For instance, a small office building would necessitate less copper than a large hospital.
Copper, which has long been a highly convenient resource for humanity, is currently facing shortages. Additionally, tariffs on imported steel are further driving up construction expenses, resulting in increased prices for new homes and contributing to elevated inflation levels. Furthermore, a shortage of global semiconductor production is also impacting the availability of certain appliances.
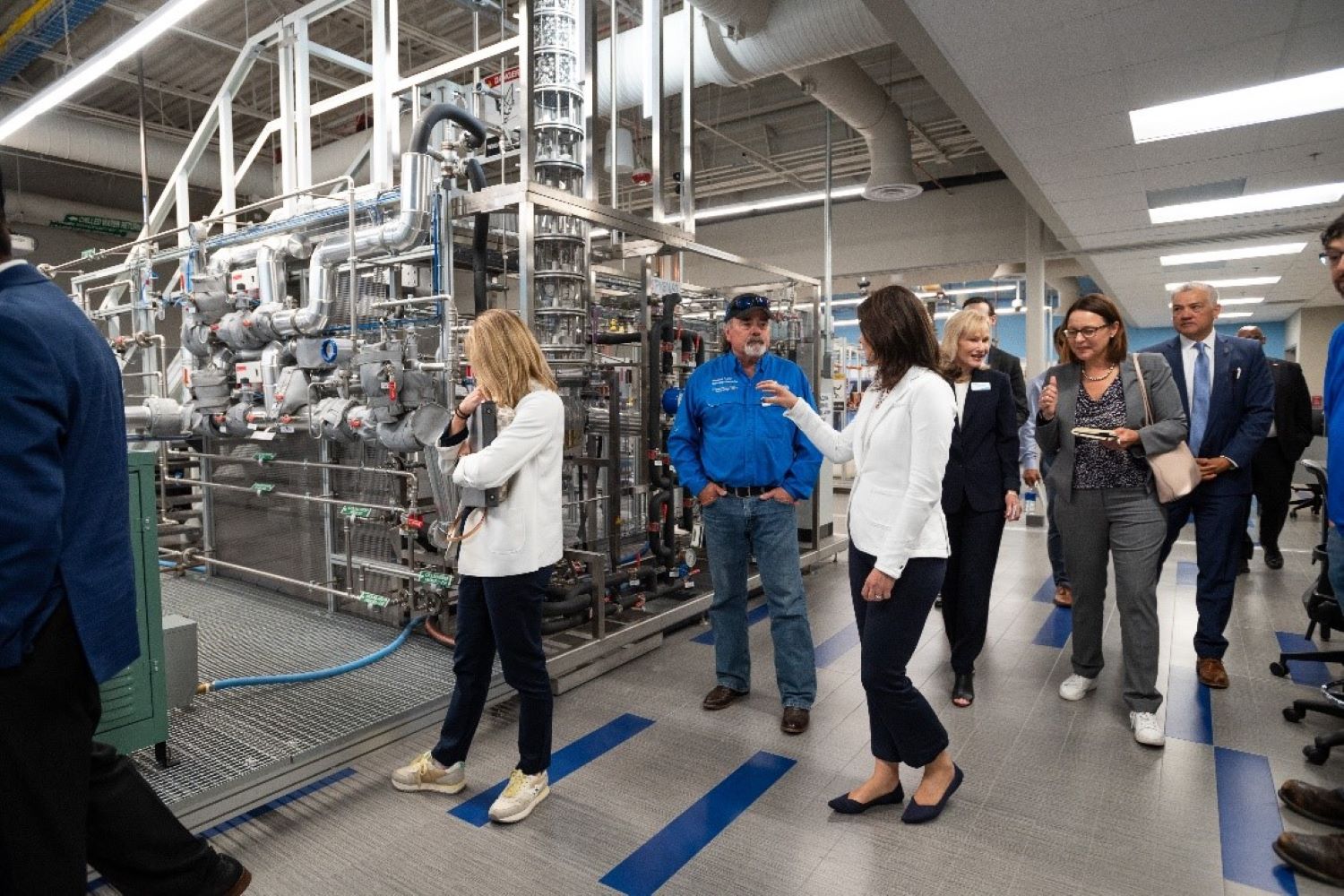
In a distinct report from the Labor Department in 2021, it was revealed that import prices surged by 1.1 percent in May. This pushed the year-over-year increase to 11.3 percent, marking the most significant rise since September 2011, up from the 10.8 percent seen in April.
“The U.S. is experiencing cost-push inflation, which historically has proven more temporary than other causes of inflation, primarily demand pull,” said Ryan Sweet, a senior economist at Moody’s Analytics.
Blocking the Path – A Green Challenge Beyond Reach?
Achieving an all-electric future is heavily reliant on copper, and a forthcoming shortage in supply could impede nations’ efforts to achieve net-zero emissions by 2050, as outlined in a recent report from S&P Global. The report underscores that without a substantial increase in copper supply, climate objectives will face significant obstacles and remain unattainable.
Copper is a vital component in electric vehicles, solar and wind power systems, as well as batteries for energy storage. According to S&P Global, an electric vehicle requires 2.5 times more copper than a traditional internal combustion engine vehicle. In comparison, solar and offshore wind power systems require two and five times more copper per megawatt of installed capacity, respectively, compared to power generation from natural gas or coal sources.
Copper is also key to the infrastructure that transports renewable energy, thanks in part to its electrical conductivity and low reactivity. Its uses include cables, transistors and inverters.
“The energy transition is going to be dependent much more on copper than our current energy system,” Daniel Yergin, S&P Global vice chairman, told CNBC. “There’s just been the assumption that copper and other minerals will be there. … Copper is the metal of electrification, and electrification is much of what the energy transition is all about.”
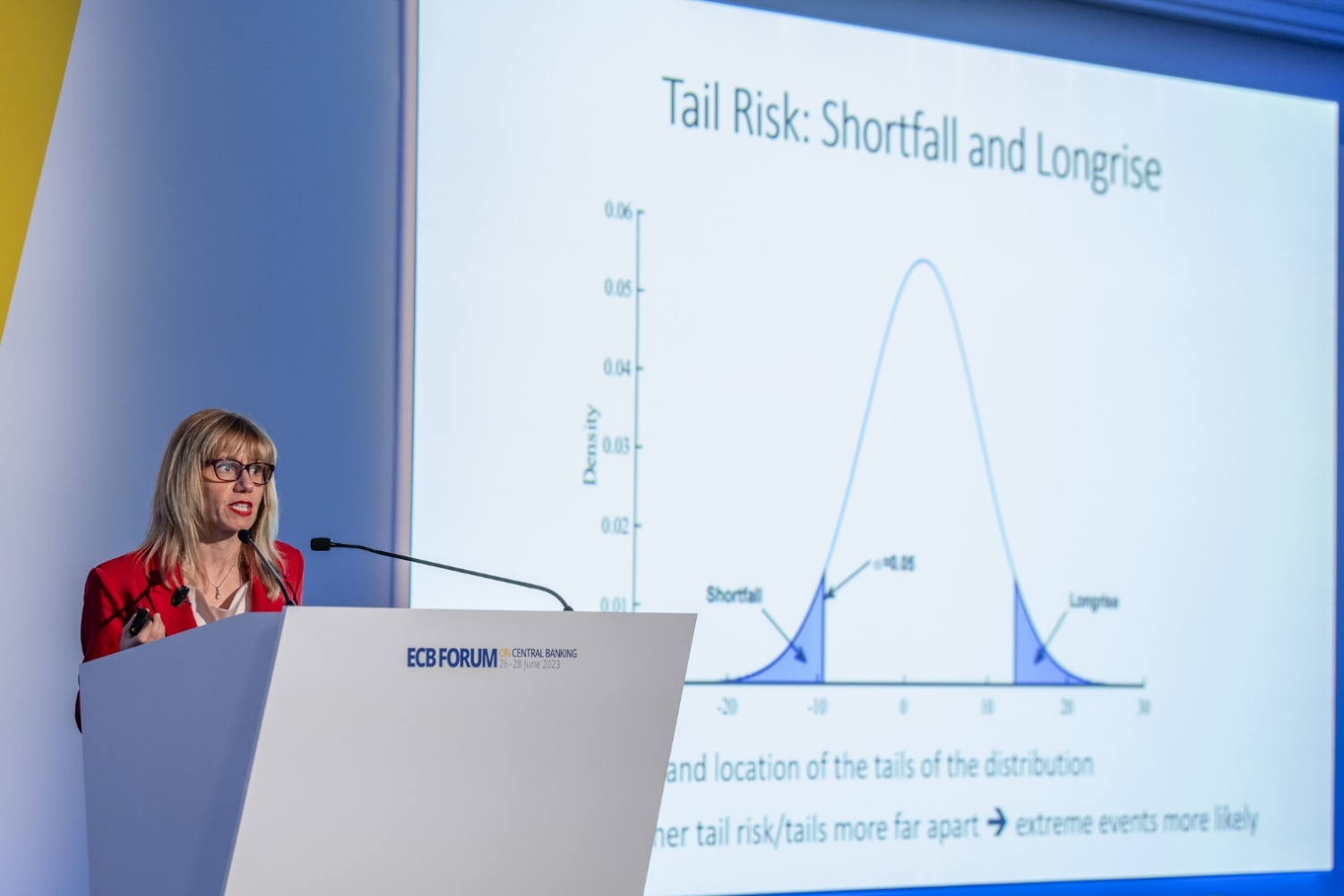
The report projects a significant surge in copper demand, nearly doubling to 50 million metric tons by 2035. By 2050, this demand is expected to surpass 53 million metric tons. To put this into perspective, S&P Global highlighted that this figure is greater than the total amount of copper consumed worldwide between 1900 and 2021.
The rapid expansion of renewable energy infrastructure will be a primary driver of this increased demand. S&P Global anticipates that the need for copper in electric vehicles, wind power, solar energy, and batteries will triple by the middle of the next decade. Simultaneously, demand from various other sectors will also contribute to pushing copper demand to unprecedented levels.
Expanding copper production is not a straightforward solution. According to the International Energy Agency, it takes an average of 16 years for a new copper mine to become operational.
In the interim, addressing the growing demand for copper can involve maximizing the output from existing mines and increasing recycling efforts.
S&P Global presents two future scenarios in an attempt to estimate the severity of the market shortfall. In the “Rocky Road Scenario,” where production largely remains unchanged, the annual supply deficit is projected to approach nearly 10 million metric tons by 2035.
In the more optimistic “High Ambition Scenario,” which involves increased utilization of mines and greater emphasis on recycling, the market is still expected to experience a deficit for most of the 2030s.
The report concludes that under either scenario, there won’t be enough supply to meet the demand necessary to achieve Net-Zero-Emissions by 2050, emphasizing the critical challenge posed by the impending copper shortage.
Bottom lines
Recent disruptions in mineral supply from regions like Panama, Chile, and Peru have somewhat receded from the immediate spotlight, as noted by Michael Cuoco, the director of hedge fund sales for metals and commodities at StoneX Group.
While some new significant mining projects have recently begun operations, and analysts at Bank of America and Citigroup anticipate a slight copper surplus for the current year, it’s important to emphasize that copper supply challenges are expected to persist in the long run.
When we consider the situation in Dallas, it may appear relatively immune to an immediate slowdown compared to some other places, as there haven’t been reports or news indicating the local impact of the copper shortage. However, given that this issue is affecting regions worldwide, it’s likely that the District will also eventually face the consequences of the copper supply challenge.