Deglobalization – Bringing Production Back to the United States
Alexander Hamilton started the industrial policy in the United States. Back then, our country wasn’t good at making things. To become stronger, we needed to make items like cannons and muskets. To encourage local production, high tariffs were put in place, making it costly to import goods. This led to American companies making more things, which played a big part in making the United States great.
And it’s true, manufacturing—the process of converting raw materials into usable goods—launched the United States as a superpower at the turn of the 20th century just as it launched China’s economy into the 21st.
However, after the end of the Cold War, what really accelerated was the economic integration of big nations. That’s when the United States started to lean on outsourcing. When countries collaborate and their economies become interconnected, it increases the likelihood of peace among them. This interconnectedness benefits the world as a whole. But is it good for America?
Outsource Manufacturing – Globalization Has Failed Us
Since the 1980s manufacturing jobs have plummeted. In the constant drive to make things cheap, factories and jobs were moved overseas. Textiles were hit especially hard.
Outsourcing has increased U.S. unemployment. Outsourced jobs are often more than the number of unemployed Americans. If all those jobs were to return, it would be enough to hire millions who are working part-time but would prefer full-time positions.
According to Robert Emmet Lighthizer, an American attorney and government official who was the United States Trade Representative in the Donald Trump administration from 2017 to 2021, he says that advocates of unfettered globalization like Bill Clinton were always wrongheaded.
He stated that, “Free trade is about price optimization and consumption. I think the important thing is production. Production leads to good jobs, good wages, and solid fundamental American communities. And if there’s a sacrifice of the price of a T-shirt or your third television set in order to have strong communities in America, that’s the sacrifice that I’m willing to make.”
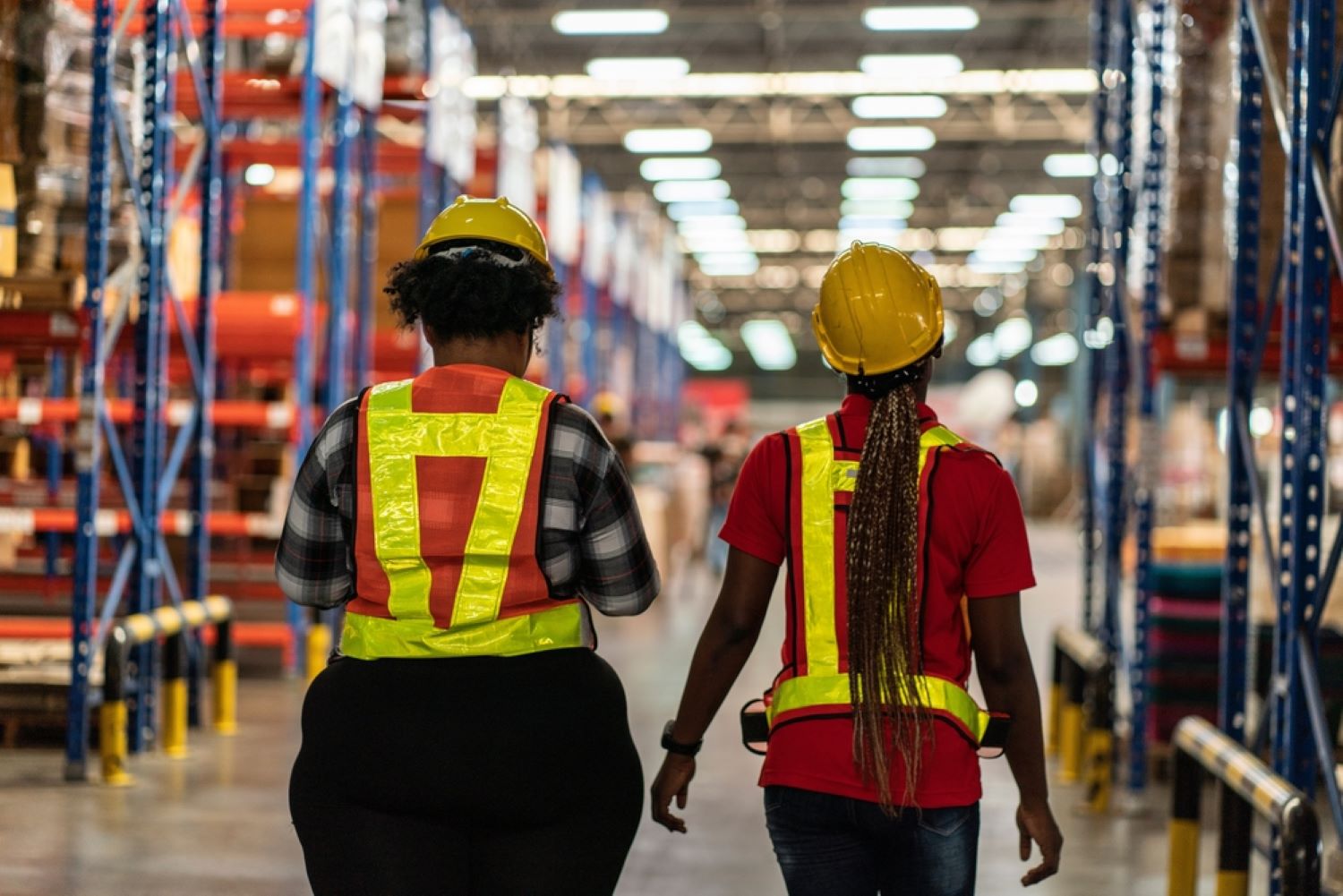
He believes the drive to globalization saw the US effectively giving away its own prosperity. Trade deals like Nafta between the US, Canada, and Mexico and also the entry of China into the WTO assumed that the US could outsource its industrial base while focusing mainly on service sector jobs, and that if global trade grew countries would become freer and more like the US.
“There was this kind of hubris that the world had changed and the market forces forever now we’re going to move us in the direction of economic growth and freedom throughout the world and all these notions, which are lovely except they just don’t exist,” said Robert Emmet Lighthizer.
He added, “I call it this trifecta of stupidity, the combination of Nafts, the WTO, and PNTR letting China have permanent preferential treatment. And the result was we lost five or six million jobs and hundreds and hundreds of thousands of manufacturing jobs and 60,000 factories. And communities all over the country were decimated. And you saw families breaking up and opioid addiction, and all of these things. It was the exact opposite of what all of these people had predicted.”
Not to mention in the years after the financial crisis, the conventional Western economic capitalist-led model came under a lot of scrutiny, given the impact that that crisis had on ordinary people. And in 2016, we saw a vote for Brexit, an exit from the European Union in the UK, and the election of Donald Trump in the US.
That, in extension, triggered a big trade war between China and the US. We’ve seen a global pandemic that has tested those global supply chains and that has led a lot of countries to rethink offshoring production. We’re seeing war in the Middle East. We’ve seen geopolitical disruption triggered by the Russia-Ukraine war. We are seeing coups in Africa, and those conflicts are leading people to question even more the benefits of globalization.
There’s a lot of uncertainty about what is ahead. That’s why we need to get home since it’s safer. The good news is that post-pandemic, there’s a new regionalization of industry taking place.
Regionalization – The Surge of American Factories
According to the Census Bureau data, record spending on manufacturing construction hit an all-time high in 2022 at $18 billion, which is even more than what was spent on building schools, health care centers, or office buildings.
And the best part? New factories are popping up everywhere, from urban cores to rural fields, desert flats to surf towns—factories are being built all over America. The growth is mainly concentrated in high-tech fields like electric vehicle batteries and semiconductors. National priorities, backed by billions of dollars in government incentives.
But that’s not all—other companies that once relied solely on lower-cost countries to manufacture are coming back home.
Yanking Out of Other Nations
Speed and flexibility are essential in today’s world. That’s why sock manufacturer Future Stitch Incorporated opened a new factory in Oceanside, California, making it the company’s first in the US. Their US factory allows them to quickly replenish stock for their retailers, which is critical in today’s market. And Future Stich isn’t the only one.
According to Kearney’s 2021 Reshoring Index, the majority of US companies with operations in China have already shifted or plan to shift production to the US within the next three years due to tariffs and supply chain challenges.
Major companies like General Motors and GE Appliances has been investing billions in US plants to bolster domestic manufacturing and create jobs.
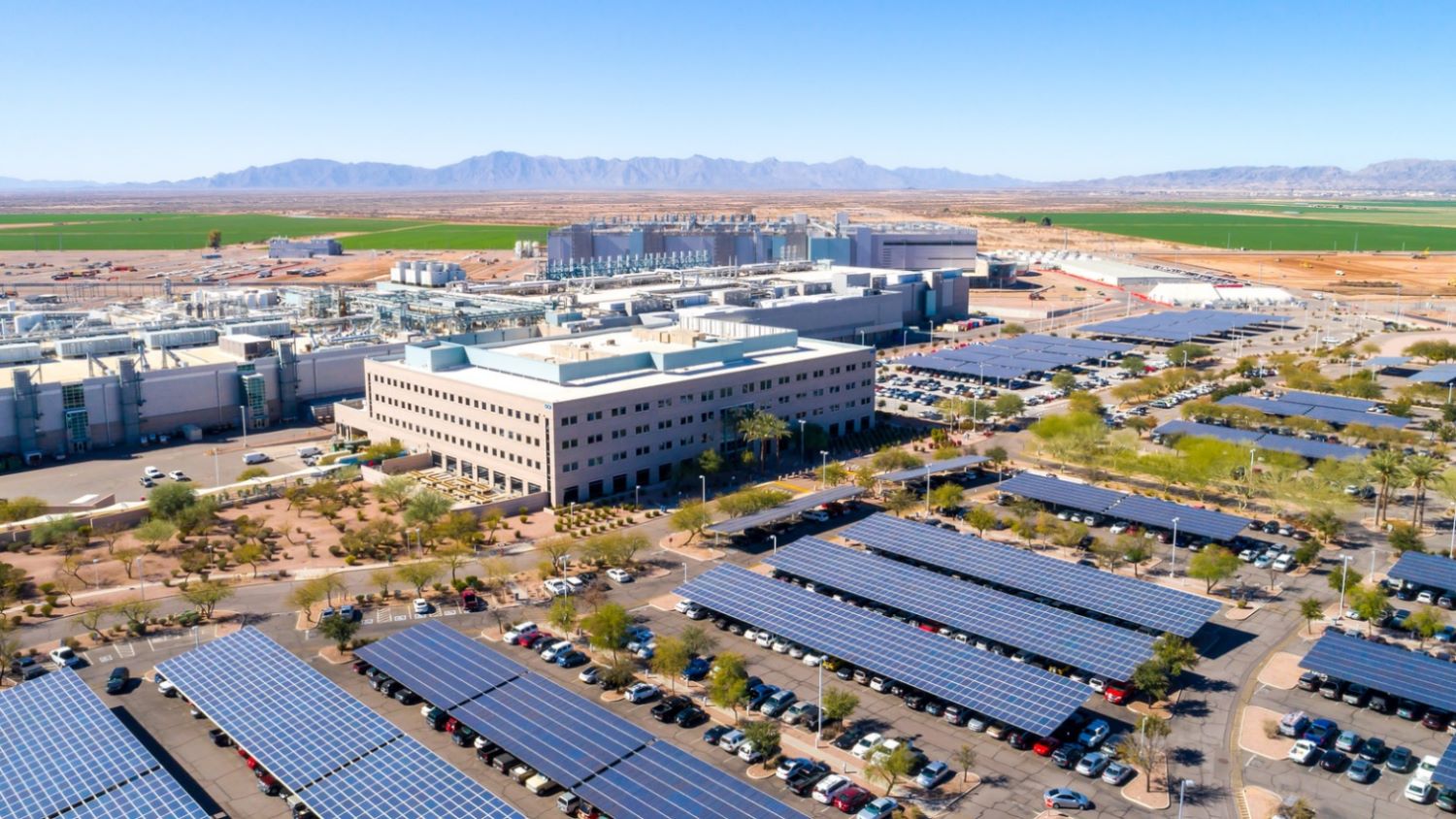
Intel has been investing $12 billion in chip factories near Phoenix to meet growing demand for semiconductors. US Steel, Nucor, Generac Power Systems, Lockheed Martin, and others has also been making significant investments in US production facilities.
Thrive in a Supportive Environment
Congress has been instrumental in this industrial resurgence by approving a subsidy package for select manufacturing industries, enhancing domestic production and revitalizing local industries.
This legislative action has had an incredible impact so far, leading to a whopping 73% increase in manufacturing plant construction in the last year. For example, a substantial $52 billion has been designated for semiconductor manufacturers to build, a figure similar in size to the defense budget of France.
In 2023, the US manufacturing industry capitalized on the momentum generated by three significant pieces of legislation that were signed into law in 2021 and 2022—the Infrastructure Investment and Jobs Act (IIJA), the Creating Helpful Incentives to Produce Semiconductors (CHIPS) and Science Act, and the Inflation Reduction Act (IRA).
Together, these laws prioritize rebuilding infrastructure, advancing clean energy initiatives, and building out the domestic semiconductor industry, while also aiming to foster job growth, workforce development, and equity.
By introducing an infusion of funds and tax incentives into US manufacturing across various sectors—including semiconductors, clean energy components, electric vehicles, batteries, and the constituent parts and raw materials of these products—the IIJA, CHIPS, and IRA have already spurred record private sector investment in the manufacturing industry.
And jobs are starting to move back. It’s about being focused not on what’s cheapest but on creating better jobs for local communities.
Bringing Jobs Back to America
Since Biden took office, US manufacturing employment has grown by slightly less than 800,000 positions, contributing to the more than 13mn jobs created as the country’s economy bounced back quickly from the pandemic. Last month, close to 13mn were employed in the US manufacturing sector, which is the highest monthly tally since late 2008.
But the industry is hurting for workers—about 800,000 more are needed, leading to concerns that labor shortages and other bottlenecks could short-circuit the boom. However, according to the National Association of Manufacturers, the manufacturing skills gap — caused by the labor market’s struggle to find workers with highly technical and manual expertise — could lead to 2.1 million unfilled jobs by 2030.
But with huge government incentives stoking the frenzy, we’re hopeful that the industry will continue to grow and flourish.
Automated Factories – Propel America Manufacturing Innovation
With a need to remain competitive on a global market, and facing a critical labor shortage, factory automation is manufacturing’s best option to meet growing business challenges.
Around the world, manufacturers are ramping up their investment in key technology areas, seeking to overcome existing pain points in their operations, improve their product and service offerings, or simply keep up with competitors that are more digitally savvy.
The installed base for the roughly $50 billion advanced robotics industry, for example, is expected to grow 6 percent per year for the next three years at least, as companies take advantage of smarter, more flexible, and more cost-effective equipment to automate more of their activities. And by 2030, Industry 4.0 applications are expected to account for almost half the total sales of 5G-connected Internet of Things (IoT) devices.
Over the coming years, US manufacturers stand to benefit from further waves of digital innovation as capital markets continue to make big investments in next-generation technologies. Annual investment in artificial intelligence (AI) has reached roughly $150 billion, and investors are pouring $250 billion into IoT technologies and $300 billion into cloud computing every year.
Artificial intelligence, machine learning, and advanced technologies are also seen as key elements in the move toward new systems that can make sense of disconnected data and bring a new level of harmony to global supply chains. And out there, many companies are working on this.
“There’s a lot of data to show that countries that adopt more automation actually end up having more jobs available for their people and higher paying jobs,” says Saman Farid, CEO of Formic Technologies, a company working to make robotic automation accessible to small and mid-sized U.S. businesses by deploying automation for a low hourly rate and zero capital investment.
“Humans are fantastic at problem-solving, at dexterity, at being creative, and at highly skilled tasks and decision making,” he says, explaining that giving factory robots the rote tasks that need to be done in a factory allows workers to upskill. “Whenever mechanization comes in, people take on more advanced and creative work.”
Rising Stars – Building the Future Backbone of America Production
Chris Power, founder and CEO of industrial automation startup Hadrian, recognized historical patterns of empires outsourcing core industries, leading to internal stagnation and decline. With a vision to address the declining US industrial base, he moved from Australia to San Francisco in 2019. Starting with $6,000 and a single contact in the US, Power founded Hadrian to leverage software and automation to make factories more efficient.
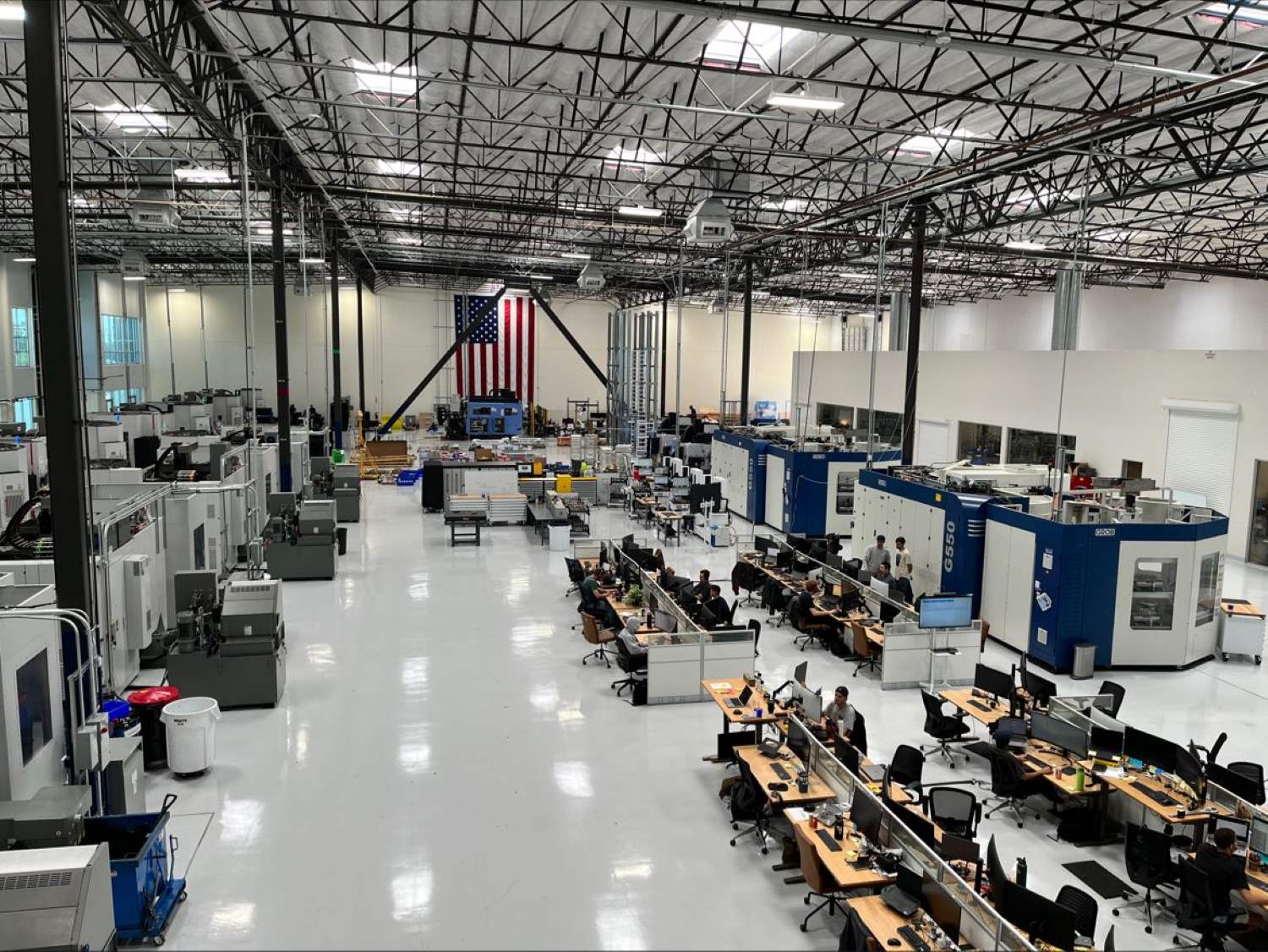
Hadrian targets high-precision CNC machining, aiming to automate labor-intensive processes. With a focus on software-driven solutions, the company has raised significant funding, including a $9.5 million seed round and a $90 million Series A in early 2022. The company’s revenue has exceeded $20 million within twelve months of launching to customers.
To meet growing demand, Hadrian plans to double its automation and software team. The company expects to be out of bookable capacity at its Torrance facility by early 2025 and intends to break ground on a second, larger facility. Hadrian is also considering alternate models, such as dedicated facilities or joint ventures with customers.
The company’s success has attracted interest from aerospace primes and Tier 1s, resulting in significant bookings and new business opportunities. Hadrian anticipates setting up at least one additional partner factory by the end of 2025.
Despite the challenges ahead, including scaling software and robotics and expanding into multiple states, Hadrian is poised to revitalize American manufacturing. With support from investors like RTX Ventures and industry players like Raytheon, the company is well-equipped to meet the demands of its customers and drive the future of manufacturing in the US.
Besides Hadrian, several key players in industrial automation are revolutionizing manufacturing processes. Advanced Integration Technology provides automation solutions for aerospace and defense assembly, while Rockwell Automation offers tailored solutions across industries like optimizing protein processing and improving newspaper printing efficiency.
ABB focuses on flexible manufacturing and smart machinery, and Honeywell pioneers warehouse automation. Fanuc is renowned for industrial robots and CNC tools, and KUKA specializes in customizable robotic systems for various industries.